From North to South, and all points in between, Blackmer® pump and compressor technologies have played a leading role for more than a century in meeting the world’s product-transfer needs
By Thomas L. Stone
In 1899, Robert Blackmer was hard at work trying to develop a more reliable, efficient alternative to the rotary gear pumps that were a prevalent pumping technology at the time. Little did he know that what he created that year – a new rotary, self-compensating pumping principle – would continue to set the standard in reliable, efficient, sustainable and cost-effective pumping performance more than 100 years later, and help optimize liquid-transfer operations in every corner of the globe, no matter the industry, the climate or the application.
Robert Blackmer recognized the shortcomings of gear-pump operation – product slippage and inefficiency as the gear teeth wear over time, creating larger clearances in the pumping chamber – and found a reliable alternative in his improved rotary vane operating principle that was the predecessor to today’s sliding vane pumps. As opposed to gears meshing together to initiate the pumping process, sliding vane pumps consist of durable “vanes” that radiate out from the pump’s central rotor and form pumping chambers during operation. As the vanes eventually wear at the tips, they simply slide further out of the rotor slots.
This ingenuous design enables the pumps to maintain their original flow rates without any appreciable loss in volumetric consistency, and makes them reliable performers in a huge array of operating conditions and climates. In 1903, a few years after the invention of the new positive displacement rotary vane pump, which was an immediate sensation, Blackmer founded the Blackmer Pump, Power and Manufacturing Company in Petoskey, Michigan, USA. The company relocated its headquarters to Grand Rapids, Michigan, in 1925 and, later, shortened its name to Blackmer. The fruits of Robert Blackmer’s vision and genius can be found today on all points of the compass as the world continues to optimize its product-transfer needs with the unquestionable help of Blackmer pump and compressor technologies.
From One Extreme to Another...
Even operators of the most sophisticated manufacturing plants know that there is no such thing as a perfect pumping environment. Perfection isn’t even a consideration when pumps are required in an oilfield or mining operation. There, facility operators just want a pump that they know will stand up to the harsh environmental conditions.
Northern Canada’s ice road – officially called the Tibbitt to Contwoyto Winter Road – is one of the most famous thoroughfares in the world, helped to be made so by the History Channel television series Ice Road Truckers. The popular show details the trials and travails involved in transporting fuel to the Diavik Diamond Mines during the harsh winter months. The ice road stretches 600 km (373 miles) with roughly 70% of its length spanning a series of frozen lakes. Because of its unique construction, the ice road is heavily regulated with the number of trucks allowed on it, and the speeds at which they can travel, strictly controlled in order to protect the ice. This means that a round trip to Diavik from Yellowknife, the capital of Canada’s Northwest Territories, can take upwards of 36 hours making the utilization of reliable pumping equipment paramount.
“I’ve used Blackmers for my entire career and wouldn’t use any other pump,” said Allen Scraba, Owner of ARS Trucking & Welding of Edmonton, Alberta, who has equipped his trucks with Blackmer TX Series Sliding Vane Transport Pumps for more than 25 years. “They are the most durable piece of equipment on my trucks. When called upon, the Blackmers perform and provide our fleet with reliable operation and great flow rates. I can’t remember a time when our pumps haven’t been able to operate due to the cold weather or harsh operating conditions.”
Scraba is so enamored of the performance of his Blackmer TX pumps that he encourages all of his contract drivers to do the same – with good reason.
“The most important part of this job is delivering on your promises,” said Scraba. “This temperature (-37ºC/-35ºF) and these conditions are very demanding. However, every good fleet owner knows that with the right equipment and proper planning, you are in a better position to succeed. That’s why we rely on Blackmer pumps.”
Some 19,300 km (12,000 miles) from the Arctic Circle, or at the other end of the globe, rests Antarctica, with a climate that is even less forgiving than that found at the Earth’s northern pole. The mean average annual temperature of the continent’s interior is -57ºC (-70ºF), while the lowest naturally occurring temperature on Earth – 89.2ºC below zero (-128.6ºF) – was recorded in 1983 at Vostok Station.
Other than the hardy penguins, whales and seals, the only creatures to call Antarctica home are the residents of the continent’s 16 Research Stations, who perform a wide variety of scientific research on such topics as astrophysics, biology, geology, meteorites and weather. Needless to say, the extreme climate dictates that equipment breakdowns cannot be tolerated. With that in mind, the residents of one of these “ice stations” rely on Blackmer F210A Series Sliding Vane Hand Pumps to ensure that their fluid-transfer needs are met – no matter how low the temperature may go. They are reliably, and confidently, using the Backmer pumps to transfer AN8 and JP5 diesel fuel, Mogas aviation fuel and kerosene.
…And Everywhere in Between
Approximately midway between the Arctic Circle and Antarctica, just south of the equator in South America, lies the country of Peru. The residents of its capital, Lima, have as much chance of building a snowman as the inhabitants of Antarctica have of sitting under a palm tree and sipping a mai tai. The average year-round temperature in Peru is 24ºC (75.2ºF) and 60% of its land mass is covered by the Peruvian Amazon jungle. Though less than 5% of Peru’s population lives in the Amazon, the area is still home to industry, specifically oil exploration and production.
This is harsh territory with almost no roads leading to the production sites. Because of that, helicopters and other small aircraft are used to transport avgas and jet fuel to base camps, where they are loaded onto river barges and transported to the exploration and production areas. When the barges arrive, they are unloaded into storage tanks. Pumping fuel from a river barge is difficult because it involves a volatile product that is constantly in motion due to the rise and fall of the river tides. The operation requires pumps that can deliver high suction lift and discharge pressures, work with low available NPSH (high vapor pressures), have self-priming capabilities and can operate in hot, humid temperatures that can exceed 32ºC (90ºF).
Meeting the needs of this critical operation are Blackmer positive displacement sliding vane pumps. The pumps not only meet the operational requirements, but also are able to maintain a nearly constant flow rate, even when the required line filters are partially saturated, an ever-present challenge in these operating conditions.
Atten-HUT!
In 1914, barely a decade after the incorporation of the Blackmer Pump, Power and Manufacturing Company, the company got a seal of approval from a pretty impressive source – the United States Military. In 2014, Blackmer will mark 100 years of being a preferred vane pump supplier to the U.S. military and, since its acquisition of System One® in 2000, a supplier of centrifugal-pump technology. More than 70 of those years have additionally been spent equipping the United States Navy with mission-critical flow solutions, while NATO Services and the French Military/Marine Services have also availed themselves of Blackmer pumping technology. Today, there are virtually no combat vessels currently in the U. S. Navy’s fleet that do not utilize Blackmer pumps.
One of the more recent and prominent examples of the Navy’s respect for, and reliance on, Blackmer products occurred in 2007 when the company’s Military & Marine Products Group won three contracts to supply pumping units for the new USS Gerald R. Ford Navy Aircraft Carrier (CVN 78). This carrier, which is slated for commission by the Navy in 2015, will be the premier forward asset for crisis response and early decisive striking power in a major combat operation. The Gerald R. Ford and subsequent Ford-class carriers will provide improved fighting capability, quality of life improvements for sailors, and reduced acquisition and life-cycle costs, according to the Department of Defense.
“We are honored to receive this contract for the USS Gerald R. Ford, especially since President Ford grew up in Grand Rapids, MI,” said Bill Erwin, Director, Military & Marine Products Group. “Since Blackmer is headquartered in Grand Rapids, everyone involved in this project is more than aware of the important role that President Ford played in our American history.”
Blackmer pumping units on the Gerald R. Ford, which underwent rigorous testing to ensure they meet shock and noise qualifications, will include sliding vane pumps that will be used in handling jet fuel and firefighting foam (AFFF).
While the U.S. Army and Navy might be its most high-profile customers, Blackmer’s Military & Marine Group also creates solutions for other marine-duty applications, as well. In 1954, construction began on the St. Lawrence Seaway, a series of canals that stretch from Montreal, Quebec, Canada, to Lake Erie and allows ships to travel from the Atlantic Ocean to the Great Lakes. As the Seaway was being built, the Saint Lawrence Seaway Development Corporation (SLSDC) commissioned the construction of the Grasse River, a derrick/crane barge that would be used as a “gatelifter” when the Seaway’s locks needed to be maintained, repaired or replaced.
Completed in 1957, the Grasse River, which is based at a docking facility in Massena, NY, USA, has been in operation for the past 55 years. In that time, the same Blackmer GL6 Model (as it was known at the time) Sliding Vane Pump has been reliably pumping the bilge water that is needed as ballast when the barge – which can lift as much as 300 tons – is performing its lock-gate maintenance duties. The age of the pump was discovered in 2011 when the SLSDC made the decision to upgrade all of the barge’s mechanical systems in order to bring them into compliance with current operating codes. As far as the barge’s owners and Blackmer engineers know, other than regular maintenance, the pump has not been out of service for more than half a century of operation.
“It’s not often that you see an old pump like that that is still operational, especially an iron pump in a water-transfer service because they can rust,” said Mike Hedgecock, Blackmer’s Engineering Services Administrator. “It surprised the heck out of us when they had a Blackmer drawing of the pump and it was dated 1956. We’ve put in a request with the contractor to return the old pump to us so we can tear it down and see what 50 years in a water application does. There’s definitely some learning we can do with this.”
A new Blackmer HXL6 Series Sliding Vane Pump will replace its distant relative on the upgraded Grasse River.
They’re A Gas
While Blackmer sliding vane pumps have long set the standard in liquids handling, in 1980 the company introduced its Compressor Division, which specializes in reciprocating gas compressors – most notably the HD and LB Series – that have become preferred equipment for the handling of liquefied petroleum gas (LPG), or propane, and other critical industrial gases. Much like the versatility found in Blackmer’s sliding vane pump units, the company’s compressors are also designed to overcome a wide variety of application requirements and climactic conditions.
Headquartered in St. Petersburg, Russia, Lenoblgaz OAO (or, in English, Lenoblgas JSC) is the main supplier of LPG and natural gas to Russia’s sprawling Northwestern Federal District. Utilizing a product-pipeline network that totals 4,436 km (2,757 miles) and six pump-station branches, Lenoblgaz supplies LPG and natural gas to a client base that includes 921 commercial customers and more than 540,000 residences in the Northwestern District, an area of bone-chilling cold during the winter months.
When Lenoblgaz determined that it needed a new compressor at its Tihvin Mezhraygas pumping station in the town of Lodeynoe Pole, which is in Leningrad Province and located about 209 km (130 miles) northeast of St. Petersburg on the Svir River, it chose a Blackmer® LB Series Reciprocating Gas Compressor. Since its installation in 2005, the LB compressor has required only one instance of maintenance, when a piston ring needed to be replaced. In fact, Lenoblgaz was so pleased with the compressor’s operation that a second LB compressor was purchased in 2009 and installed next to the original.
Halfway around the globe is the North African nation of Algeria, which is the world’s second-largest exporter of LPG. In 2007, the Algerian government was looking to upgrade the compressor technology that was used at the country’s 20 state-run LPG terminals. In a procurement process that took more than 18 months, by 2009, Blackmer LB Series Reciprocating Gas Compressors were in operation at all of Algeria’s LPG terminals.
“The decision to place that first LPG compressor order with Blackmer was based on the quality of the products and brand-name recognition,” said Al Buhler, Blackmer’s International LPG Sales Manager, who negotiated the compressor sale with the Algerian government. “This was an excellent example of really cooperating with a government entity and being successful by making them feel very comfortable with the product.”
Closer to home, Blackmer pumps and compressors are playing a prominent role in helping to ensure the safety of Michigan’s propane industry. In 2009, the Michigan Propane Gas Association (MPGA) created the Propane Emergency Response Network (PERN). The goal of PERN is to supplement the fire training that is offered to the state’s first-responders, many of whom do not have the appropriate training to handle major LPG emergencies.
The heart of the PERN program is a fleet of emergency-response trailers that are fully equipped with Blackmer pumps and compressor units, as well as power units, hoses and other accessories that are typically required for handling propane-related emergencies. The trailers are strategically located in five different fire districts in Michigan. Each consists of regionalized propane teams who are volunteers that have been trained specifically to handle propane emergencies. Working hand in hand with police and fire departments in the state, the goal of PERN is to reduce the response time to any propane-related incident in the state.
“I’m really excited about the opportunity to develop this level of added safety and knowledge about propane in the state of Michigan,” said Brian Lincoln, MPGA President at the time. “Some of the new safety training in the PERN Program even involves live, simulated propane fires using a special trailer and equipment designed for this purpose.”
A Centrifugal Force
System One® Centrifugal Pumps have been a Blackmer product line since 2000 and they have already earned a reputation for high performance in an array of arduous operating conditions. The mining industry in the Australasian countries of Australia, New Zealand and New Guinea, as well as the numerous neighboring Pacific Ocean islands, battles harsh, rugged, trying conditions on a daily basis. That means the need for pumps that can live up to the stresses and challenges associated with day-to-day mining operations.
Resource Equipment Limited (REL), based in Welshpool, Western Australia, specializes in the creation of mine dewatering systems that are designed to draw water and other liquids used and produced during mining operations up and out of the mine. Industrial pumps are key to these operations, with the most efficient and effective way to eliminate the water is by utilizing an evaporative process.” In this scheme, the water from the mines is fed via pumps and piping system to a set of evaporators, which turn the water into a fine mist that is blown by a series of oscillating fans into, or over, a large body of water.
REL has determined that the best pump for use in these applications is the Blackmer System One Model LD17 Centrifugal Pump.
“The System One meets the needs of the types of applications in which REL specializes because it is constructed with a heavy-duty, solid, low-deflection shaft that prevents common vibration damage, and provides greater stability at the mechanical seal area to improve seal life and extend bearing and shaft life,” said James Lee, Product Specialist for Blackmer.
Since installing the first of the water-evaporation systems to feature LD17 pumps in late 2010, REL and its end-user customers have experienced none of the frustrating breakdowns and operational inefficiencies that dogged the previous centrifugal pumps that they were using.
Conclusion
Product handling and transfer, no matter the continent or the climate, is the lifeblood of literally thousands of global industries, and is a key consideration in military operations. Only the companies that optimize their product-handling capabilities reach the level of success that they envision for themselves and their customers. Helping so many of these companies realize their goals for more than a century has been Blackmer, which was not only at the forefront in perfecting the rotary sliding-vane principle, but has continued to produce the industry’s most reliable pump and compressor technologies utilized in crucial applications around the world.
About the author:
Thomas L. Stone is the PSG Director of Marketing and is based at Blackmer’s Global Headquarters in Grand Rapids, MI, USA. He can be reached at tom.stone@blackmer.com. For more information on Blackmer’s full line of pumps and compressors, please go to blackmer.com or call (616) 241-1611. Blackmer is a member of Dover Corporation’s PSG®, Downers Grove, IL, USA, which is comprised of leading companies such as Almatec®, Blackmer®, EnviroGear®, Griswold™, Mouvex®, Neptune™, Quattroflow™, RedScrew™ and Wilden®. You can find more information on PSG at psgdover.com.
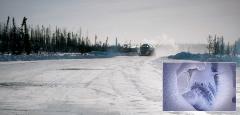
Blackmer sliding vane transport pumps (see insert) have been braving the cold on Northern Canada’s ice roads for more than 25 years.
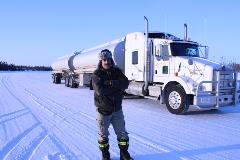
According to Allen Scraba, Owner of ARS Trucking & Welding of Edmonton, Alberta, the Blackmer TX Series Sliding Vane Transport Pumps operate flawlessly in extreme cold conditions.
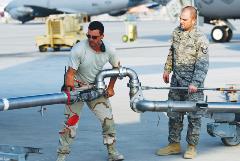
Blackmer’s Military & Marine Products Group supplies pumps to the U.S. Military, NATO Services and French Military/Marine Services.
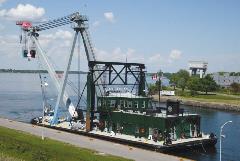
The same Blackmer GL6 Model Sliding Vane Pump has been used to pump bilge water on a barge in the St. Lawrence Seaway for more than 50 years.
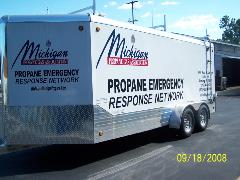
Michigan’s Propane Emergency Response Network (PERN) program employs a fleet of emergency trailers that are equipped with Blackmer pumps and compressor units.
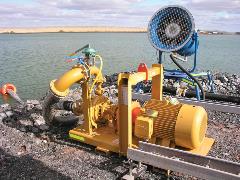
The heart of this water evaporation system in Australia is the Blackmer System One® centrifugal pump.