Yellow Cab Upgrades to Blackmer® Equipment as it Continues to Reap the Benefits of its Propane-Powered Taxicab Fleet in Las Vegas
By Thomas L. Stone
With the majority of its customer base comprised of the millions of tourists and business people who flock into and out of the city on an annual basis, it’s no surprise that the taxicab industry in Las Vegas, NV, is a competitive one. Nine cab companies run a 24-hour loop between McCarran Airport, the hotels on the Strip and downtown, and the lush golf resorts that inhabit the sprawling city’s outer edges, vying for the transportation dollars of the casino-goer, honeymooners, or the business professional attending one of the city’s thousands of conventions.
Only one of these companies, however, has made a longterm commitment to protect the city’s atmosphere from harmful exhaust emissions as its iconic bright-yellow, white with distinctive black-and-white checkerboard trim, and white-with-green-roof cabs tour the streets on the lookout for fares.
In The Beginning…
Nearly 30 years ago, the Yellow Cab Company made the conscious decision to convert its entire fleet of taxicabs so that they would run on environmentally friendly propane. When Yellow Cab acquired fellow cab companies Checker in 1984 and Star in 1986—in the process creating the umbrella company Yellow-Checker-Star Transportation, Nevada’s largest taxicab business, with the three companies continuing to operate autonomously—all of the taxis in their fleets were also converted to propane. What’s really surprising is not that YCS chose to eschew traditional gasoline for its combined 800-taxi fleet—550 of which are on the road at any one time—but that in the ensuing three decades, not one of its competitors has fully committed to going the propane route, despite the identifiable benefits that have been realized by both the environment and YCS Transportation’s bottom line since the switchover.
“This is just a win-win situation,” said Aaron Cohen, Nevada Yellow-Checker-Star Transportation’s Director of Automotive Services, who has been with the company for nearly 24 years. “It helps the environment since the cabs put out less pollutants than gasoline cars, and propane is cheaper than unleaded gasoline, so you get a healthy environment and save a few dollars in the process. Our cabs are the only ones to run on propane, though there is a lot of cost involved in putting in the infrastructure, plus the cost of converting the cars; that’s quite a commitment.”
That commitment involved reconfiguring its facility so that propane-fueling stations could be installed. With the facility updated, the cab drivers just pull up to a pump like they would for a fill-up at a traditional gasoline station, except that propane is the fuel of choice. On weekdays, the fleet will burn through around 9,000 gallons of propane, with the consumption rising to 12,000 gallons per day on weekends. To keep up with the demand, YCS gets at least a daily 9,000-gallon delivery of propane that is stored in its two 60,000-gallon storage tanks.
While this use of propane is good for the environment, Cohen recently noticed that the propane fuel pumps weren’t delivering the level of efficiency that he was hoping for. On closer inspection, he determined that there was a glitch in their operation that led to increased maintenance concerns, mitigating the positive effects found in the use of propane.
“We had three double-pump fueling locations—a total of 6 pumps—and they were pumping adequately, but there was a reliability issue—they kept burning up at an unbelievable rate, at least once every other month, because there was too much cavitation,” said Cohen.
In the search for a solution, Cohen turned to Meeder-Ransome Equipment Company, Fresno, CA, Yellow-Checker-Star Transportation’s propane-equipment supplier and a company with a 55-year commitment to the LP gas industry. The decision was made to upgrade to a Model LGLH2A Sliding Vane Pump from Blackmer®, Grand Rapids, MI. This model was chosen because it features a cavitation suppression liner that reduces the amount of cavitation and noise versus the previous pumps. Cavitation is produced by the sudden collapse of vapor bubbles. LGL Series pumps allow a controlled amount of fluid at discharge pressure to bleed back toward the suction of the pump. This allows any vapor bubbles to be collapsed over a longer period of time, resulting in improved flow, less vibration, less noise and less wear on the pump. “We took out the 6 pumps and replaced them with 3 Blackmer high-differential pumps and by-pass valves. So far it’s solved our problem. We chose these pumps for their reliability, longevity, and safe and efficient operation,” said Cohen. “Blackmer pumps can fill six or seven cars at a time at 16 to 17 gallons a minute and it doesn’t slow down even when the fuel island is full. Time is money in our business and that’s a huge time-savings for our type of operation”
In addition to the cavitation suppression that the LGLH2A pumps provide, their sliding-vane design self-adjusts for wear to maintain desired flow rates, while worn vanes can be easily replaced without removing the pump from the piping system. The pump’s other benefits include ductile-iron construction with an internal relief valve; replaceable casing liners and end discs; self-priming and dry-run capabilities; symmetrical bearing support for even loading and long life; and adjustable relief valves that protect against excessive pressures.
System Improvements
As mentioned, choosing propane has brought a lot of benefits to Yellow Cab and Las Vegas, but there had always been a small blind spot in an operation of this nature. Whenever the cabs needed to be brought in for routine maintenance, or if an older vehicle was being taken out of service, before any work could be done on them, the propane tanks would need to be evacuated. For years, it was an accepted part of this process that a small amount of propane vapor would inevitably escape into the atmosphere during evacuation.
Knowing that there had to be an efficient, effective way to not only prevent atmospheric venting of the propane, but to also recapture any product that might escape, then store it and reuse it, Yellow Cab began the search for an evacuation system that would meet its needs, without much initial success.“I was kind of shocked,” said Cohen.
“Well over a year ago, we were looking into acquiring an evacuation and vapor-recovery system and found out that, basically, nobody builds them. We did have a company start to make us an evacuation system, but they never got it right.”
At a crossroads, Cohen turned again to the experts at Meeder-Ransome. “They were trying to use a system where they’d bring in the cabs that needed service and have to suck the propane down far enough to make it safe to work on, about 5 psi,” explained Angrest Harris, Vice President of Engineering for Meeder-Ransome. “The cabs would come in with pressures much higher than that and they would connect them to the system and try to pull down the pressure, but the system didn’t work; it was burning up the compressors too quickly.”
After analyzing the existing setup, Harris determined that a number of changes would need to be made. In the end, the redesigned system now features a single-stage gas compressor, larger receiver tanks and fine-tuned controls that allow the pressure in propane tanks to be reduced to the desired 5 psi in the shortest time possible.
“A company of that size is concerned with safety and they needed a system that allowed them to do these tank evacuations safely while reducing the hazards of having some propane escape into the atmosphere,” said Harris. “They also needed a system that worked in a controlled environment. Now, the cabs come in at 100 to 200 psi, the tank is connected to the receiver vessel, we equalize the system and in 5 to 10 minutes we’re able to take it down to 5 psi.
“Basically, what we’re doing is taking a bigger receiver tank, filling this tank up, and dropping the pressure in the system to get it to liquefy. Then, when there’s so much liquid in the tank, we equalize the receiver vessel with the large storage vessel so that there’s no differential pressure, and pump out the liquid to their storage tank.”
Playing a critical role in this process is an LB161 Reciprocating Gas Compressor from Blackmer. These oil-free compressors have been designed to deliver high efficiency in handling propane and are ideal for vapor-recovery applications. Among the many features of the LB161 Series are standard ductile-iron cylinders and heads; O-ring seals between the cylinder and head; case-hardened steel valves and seats with stainless-steel discs and springs; a one-piece piston; self-lubricating filled PTFE piston rings and piston rod packings; pressure-lubricated crankcase; and wear-resistant crosshead assemblies.
“If we have to change the valves on a tank, or perform any type of maintenance, we just take the cab to the evacuation setup,” said Cohen. “Not too many years ago, if we had to drain a tank for any reason, it wasn’t good for the environment and good for the company because we would lose a little propane into the atmosphere. Now, when we have to evacuate a tank, the propane goes into the intermediate tank and then goes into one of our two 60,000-gallon storage tanks and gets reused for fuel.”
Conclusion
It’s safe to say that when it came to making a commitment to the environment through the use of propane in its taxicab fleet that Yellow Cab was ahead of its time. With the combined fleet of YCS Transportation cabs logging more than 50 million miles per year in the Las Vegas area, estimates say that Yellow Cab’s use of propane—which produces practically no sulfur emissions and releases carbon monoxide at levels 60-percent lower than gasoline—means that there are 800 less tons of carbon monoxide emissions and 800 less tons of particulate matter introduced to the atmosphere per year by those cabs.
YCS also proudly points out that all of its propane-powered taxis are equipped with enhanced safety features, including slam valves in the tanks and emergency shut-off switches that ensure that the propane is contained in case of an accident. Aiding in these safety and environmentally conscious efforts are the LGL Series pumps and LB Series reciprocating gas compressors from Blackmer, which are providing Yellow Cab with the operational efficiencies, cost savings and environmental friendliness that the company has built its reputation on for the past 30 years.
“So far, the Blackmer pumps are working out very well, and the new evacuation system with the Blackmer compressor has been working great,” said Cohen. “Meeder-Ransome did a great job engineering the system and the company has been a pleasure to work with.”
About The Author
Thomas L. Stone is the Director of Marketing for Blackmer, an operating company within Dover Corporation’s PSG. You can find more information on PSG at psgdover.com. Mr. Stone can be reached at tom.stone@psgdover.com. For more information on Blackmer’s full line of pumps and compressors, please go to blackmer.com or call (616) 241-1611.
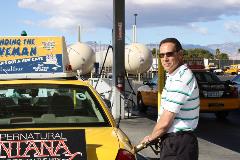
Aaron Cohen fuels one of the taxis with propane in a safe and efficient manner at the busy fueling island. On weekdays, the fleet will burn through nearly 9,000 gallons of propane, with the consumption rising to 12,000 gallons per day on weekends.
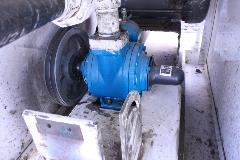
The facility replaced 6 pumps with 3 LGLH2A pumps. Blackmer pumps were chosen due to their reliability, cavitation suppression and ease of maintenance.
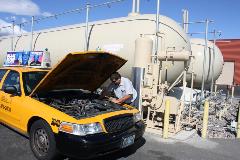
Kevin Ash, Supervisor – Propane Specialist for YCS, uses the vapor-recovery system designed by Blackmer distributor Meeder-Ransom to draw down the vapor level in the taxi prior to service. The vapor-recovery system features a LB161 Series compressor.
Looking Ahead
While Yellow Cab set the standard in environmentally conscious forward thinking by converting its taxicab fleet to propane three decades ago, the “green” movement is rapidly catching up to nearly every industry across the globe. Long gone are the days where operating practices that have been deemed environmentally harmful will be tolerated. From more-efficient light bulbs to painting factory roofs white to reduce heat retention in the summer, companies are looking for ways to reduce their carbon footprint.
One area that is coming under increased scrutiny is the handling and storage of such vapor-based petroleum products as natural gas and propane. For years, it has been a fact of life—if a propane tank needs to be evacuated, some small amount of propane would escape into the atmosphere. If the U.S. Environmental Protection Agency has anything to say about it, that will not be allowed to happen in the very near future.
“The EPA is serious about reducing the amount of Hazardous Air Pollutants (HAPs) being released into the atmosphere and is becoming aggressive in the determination of the exact damage being done by these gas emissions,” said Gary Israel, Regional Sales Manager for the Pump Solutions Group (PSG™), of which Blackmer is a member. “Some of these studies being done even consider that HAPs are actually doing more damage to the ozone layer than is CO2.”
Realizing this, Blackmer is promoting its lines of LB, HD and NG Series Reciprocating Gas Compressors as necessary components in an effective tank-evacuation and vapor-recovery system. Yellow Cab has gotten the message and recently installed an LB161 compressor at its maintenance facility, where the propane tanks on its cabs are evacuated prior to service, with the recovered propane transferred to a storage tank for later fuel usage.
“We’re doing our part to keep the world ‘green’,” said a proud Aaron Cohen, Nevada Yellow-Checker-Star Transportation’s Director of Automotive Services.
Vapor-recovery unit currently in use at YCS facility, featuring an LB161 Series Compressor from Blackmer.