Reciprocating gas compressors establish a new standard in natural-gas vapor recovery thanks to their environmental and economic benefits
By Glenn Webb
Introduction
Recovering methane gas vapors from tank batteries is not a new application for most owners and operators of oil-and-gas production companies and crude-oil storage-tank facilities. However, the economics for justifying the installation of Vapor Recovery Units (VRUs) on tank-batteries vary with the size of the storage facilities, as well as the prices at which the gas is selling. Also to consider, in addition to the regulations already required by the Clean Air Act (CAA), is the fact that there are increasing environmental regulations being considered by governmental entities such as the U.S. Environmental Protection Agency (EPA), regulations that can call for a significant reduction in the uncontrolled release of methane gas to the atmosphere.
Therefore, companies that want to take a proactive approach to reducing the amount of uncontrolled releases of Hazardous Air Pollutants (HAPs) into the environment are taking another look at using non-lubricated reciprocating gas compressors for vapor-recovery applications. Tank vapor-recovery applications, a market once thought to be off limits to non-lube designs due to the higher cost of oil-free (non-lube) reciprocating machines, are now becoming an economically feasible and environmentally smart choice for many operators.
Blackmer, Grand Rapids, MI, USA, a Dover Corporation company and a member of the PSG, Redlands, CA, USA, is a manufacturer of sliding vane, centrifugal and peristaltic (hose) pumps and non-lubricated oil-free reciprocating gas compressors. Blackmer entered the reciprocating compressor market in the late 1970s. Seeing a great opportunity to complement its existing success in the propane and NH3 markets, where its sliding vane, positive-displacement pump technology had been used for many years, Blackmer developed a complete line of non-lube reciprocating compressor designs for use with a wide range of liquid-transfer and vapor-recovery applications such as railcar and transport tank loading and unloading, and various gas-evacuation operations.
A New Approach
For many years, the accepted method of unloading liquefied gases from railcars or transport tanks was by removing the liquid with a pump. Several pumping technologies were used for this task, including gear pumps, centrifugal pumps and sliding vane pumps, just to name a few. Railcars posed a particular difficulty for pump users because the tank openings are located on top of the tanks. This created difficult pumping conditions because the pumps have to “lift” the product in order to remove it. While each technology had its strong points, none of them could pump 100% of the liquid from the tanks.
Even attempts to get close to emptying the tank via pump usage could result in significant damage to the pumping equipment because the pump would “starve” for liquid as it neared the bottom of the tank.
Eventually, the concept of using a vapor compressor to unload the product became a reality. This process, commonly known as “liquefied gas transfer”, dramatically changed the way product was transferred from pressurized tanks with top openings. By using a non-lube compressor, not only could the liquid be emptied from the tanks without the concern of equipment damage, but the vapor compressor could also recover the “liquid heel” in the bottom of the tank that pumps could never recover by pumping
That ability alone made the use of compressors more user-friendly than pumps, but the gas compressor also offered one more huge benefit to operators. By adjusting a couple of valve positions in the piping, the compressor’s flow direction could be reversed and the compressor could now recover almost all of the gas vapors that were in the tank.
It turns out that there was gold, in the form of recoverable product, in those nearly empty tanks.
Several hundred additional gallons of product can be recovered by the compressor from every large tank that is unloaded. The compressor’s ability to transfer liquid and recover liquid heels and tank vapors proved to be a huge economic savings for most companies transporting and/or selling various liquefied gases like propane.
The Evolution Continues
Today, Blackmer compressors have evolved into a full range of products that cover a broad range of markets, including liquefied gas transfer, vapor-recovery and gas-boosting applications for a wide range of gases. Handling hazardous, toxic or flammable gases is what Blackmer compressors were born to do.
In addition, Blackmer’s oil-free design provides truly unique features that were at one time considered unneeded and unimportant in the natural gas market. Now these features have a very strong environmental appeal while still offering the best tank-emptying mechanics.
■ Oil-free designs do not add any additional contamination to the gas being handled or recovered.
■ Maximum control of gas leakage from the compressor is achieved because of the compressor’s full distance-piece compartment and piston rod seals. The two sets of rod seals create a compartment between the process gas and the lubricated crankcase, which will provide leakage control and minimize any leakage to the crankcase or the atmosphere.
This design advancement ensures that oil-free reciprocating gas compressors are an environmentally friendly and safe method to move and recover gas and vapors. In today’s tank vapor-recovery applications these are both important features that many other designs do not have.
The Challenge of Condensate
Condensate can form inside the compressor due to the wide range (mix) of hydrocarbons that can be in the gas stream. Formation of condensate inside the compressor is never good. When the gas is compressed, heavier hydrocarbons and small amounts of water vapor can form. Compressors that do not have a distance piece will let the condensate leak directly into the crankcase. This condensate damages the lubricating oil quality and will lead to significant bearing damage or a complete failure of the power frame.
System designers (packagers) provide skid designs to minimize liquids forming in the gas stream.
Non-lube reciprocating gas compressors help control condensate that may form inside the compressor. System designers should maximize their efforts to minimize liquids in the gas stream. Blackmer oil-free compressor designs do provide a means to control small amounts of condensate by collecting the condensate in an area of the compressor called the distance-piece compartment. Easy operator access to this compartment allows the user to empty the distance-piece compartment regularly. The distance piece can also be vented to a safe disposal area when available. This design gives the distance piece the ability to provide an effective means of controlling condensate.
While single-compartment distance-piece designs will generally satisfy most design requirements, Blackmer also offers triple-packed (two-compartment distance-piece models) for applications where leakage control is extremely critical. These proven designs have been used in industrial and chemical plant applications for many years.
Conclusion
As noted by Carl Jones, General Manager of Odessa Pumps, Houston, TX, a long-time Blackmer distributor headquartered in Odessa, TX, “Environmental compliance managers at many of the larger oil-and-gas companies are beginning to see the need to further reduce fugitive emissions. Going green is not going to go away.”
In a December 2009 Endangerment finding, which was reported in a “Washington Watch” article in the January 2010 issue of American Oil and Gas Reporter, EPA Administrator Lisa Jackson found that “the current and projected concentrations of the six key, well-mixed greenhouse gases—carbon dioxide, methane, nitrogen oxides, hydrofluorocarbons, perfluorocarbons and sulfur hexafluoride—in the atmosphere threaten the public health and welfare of current and future generations.” Process-system designers at most large gas companies are developing improved gas /liquids control technology that minimizes the condensing of liquids during the gas-recovery process. However, none of this progress addresses the environmental issues inherent in leaking methane gas and other HAPs that are introduced into the atmosphere.
Reciprocating oil- free gas compressor designs like those offered by Blackmer provide a safe and effective method to control potentially dangerous HAPs. In addition to their environmentally-friendly benefits, reciprocating oil-free gas compressors provide economical advantages to operators due to their ability to efficiently recover gas from crude storage tanks, and well head gas applications.
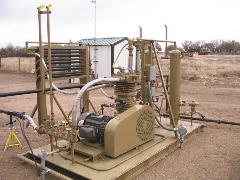
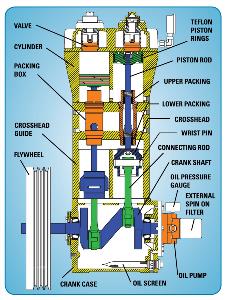
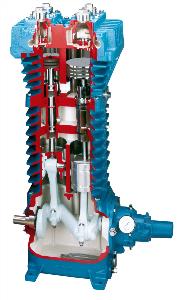
Blackmer HD Series heavy-duty, oil-free, reciprocating gas compressors.
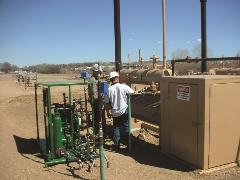
Non-lube reciprocating gas compressors help control condensate that may form inside the compressors. Blackmer compressor designs provide a means to control small amounts of condensate by collecting it in an area of the compressor called the distance-piece compartment.
[Sidebar]
An Answer to Energy Concerns
Often lost in the ongoing national debate about whether or not relying on foreign sources of energy—namely crude oil— is putting the nation’s security at risk, as well as which forms of renewable energy might be the most feasible if we were to lessen our reliance on petroleum products from foreign sources, is the fact that, according to the CIA World Fact Book 2009, the United States is the world’s second-largest producer of natural gas.
In 2009, the U.S. produced nearly 546 billion cubic feet (Bcf) of natural gas, trailing only Russia’s 654 Bcf. When it comes to the consumption of natural gas, the U.S. outranked everyone by consuming almost 653 Bcf in 2009, which is more than 150 Bcf more than the countries of the entire European Union, while Russia consumed only 481 Bcf. According to the U.S. Energy Information Administration, at the conclusion of January 2010, the United States had more than 2.4 Bcf of working natural gas in storage.
With this much natural gas in development and already on hand there is the potential for a lot of vapors to be released to the atmosphere. The main area of natural-gas vapor loss is in the oilfield. Natural gas is a by-product of oil exploration. As the oil rushes up a wellbore to the Earth’s surface, it brings along some amount of natural gas. At the wellhead, the natural gas is separated from the crude oil. It’s at that time that it is most likely to reach the atmosphere, most often as the equipment at the tank storage battery is vented.
There are numerous other areas along the natural-gas supply chain where it can also enter the atmosphere. Some can occur as the gas is transferred from a mode of delivery to a bulk-storage tank. Once the gas reaches the consumer market, there are also many escape points. All of these result in Hazardous Air Pollutants (HAPs) reaching the atmosphere, a previously acceptable practice to which the U.S. Environmental Protection Agency is beginning to pay closer attention.
Also add in the fact that any product that is lost to the atmosphere can never be sold, and it’s easy to see that there are economic factors in play as well when it comes to natural-gas vapor recovery. That’s why many natural-gas producers, bulk-plant operators and end-user distributors are beginning to investigate the ways that a vapor-recovery system can enhance their operations.
Blackmer, a recognized world leader in providing transport and transfer equipment for a wide array of commodities, has developed its lines of Oil-Free Reciprocating Gas Compressors with the needs of the natural-gas industry in mind.
More and more operators are discovering that these compressors should be an integral part of any vapor-recovery system.

When crude oil is gathered and stored in a tank battery the chance for vapor escaping is very high. Vapor-recovery systems that feature Blackmer Oil-Free Reciprocating Gas Compressors can capture these vapors providing increased safety and additional revenue for the producers.