SNP Series Sliding Vane Pumps from Blackmer® deliver the efficiencies required for complex product transfer applications in global soap and detergent operations
By Tom L. Stone
Introduction
The evolution of soap and detergents has come a long way since the early days when boiled fats, oils and ashes of animals were combined to form a useful cleaning product and when “washing” clothes meant taking them down to the local river and beating them against a rock.
The first quantum leap in soap and detergents development came almost a century ago when shortages of fats during World War I sparked the invention of synthetic detergents. That led to full-scale soap and detergent production in the post-war years and the creation of the first “built” detergents – those that contain surfactants and builder combinations – in the years immediately following World War II.
Those periods of innovation helped create and mold the worldwide soap and detergents market that we recognize today, a market of diverse products such as fabric softeners, automatic dishwasher detergents, shampoos and oven cleaners. Still, the soap and detergents industry continues to evolve, with newer products such as liquid soaps and body washes becoming more popular than traditional bar soaps, while a growing variety of scents have almost completely replaced the traditional pine or institutional ammonia smells.
One area where soap and detergents products have really aided the consumer is in convenience, exemplified by the increasing availability and use of disposable “wipes” for a number of cleaning purposes. Once intended solely for use as cleansing sheets for babies, the universe of the cleaning wipe has grown to include those that can be used to dust, wash, disinfect or sanitize any number of different surfaces, all from a convenient plastic tub. For example, a recent survey conducted by the Soap and Detergents Association revealed that 71% of consumers in the United States purchase cleaning wipes, 77% keep cleaning wipes in at least two rooms of their house and 35% use some form of cleaning wipe on a daily basis.
The ongoing pace of product innovation requires manufacturers of soap and detergents to be versatile enough to not only efficiently produce their current products, but also the “next big thing” that may come into prominence. This white paper will highlight the pumping technology that has the reliability and versatility to handle many of the different types of fluid-handling operations that are characteristic of the global soap and detergents manufacturing process, whether traditional or “new and improved.”
The Challenge
Estimates put the revenues of the global soap and detergents market at US $120 billion (85 billion) a year. More than half of the revenues come from the laundry and fabric detergents segment, while the household cleaner, dishwashing cleaner and personal cleaning products segments account for between 1⁄10 and 1⁄5 of global revenues on an annual basis. Broken down further, the EMEA (Europe, Middle East and Africa) and Asia-Pacific regions each account for roughly US $45 billion (31 billion) in annual soap and detergents revenues, with the Americas contributing US$30 billion (21 billion) in annual revenues. Laundry and fabric detergents are the most commonly used in all three regions, with the Americas and EMEA having higher sales of household cleaners and Asia-Pacific paving the way in personal cleansing products.
As mentioned, with the growth and expansion of the soap and detergents markets in all regions of the world, the four segment designations – laundry and fabric washing, household cleansers, personal cleansing products and dishwashing cleaners – now cover a wider array of actual products. For instance, the laundry detergent segment has grown to include stain removers, fabric softeners and presoaks, while household cleaners now run the gamut from multi-surface cleaners to rug shampoos to drain openers.
Therefore, an underlying challenge for any large-scale soap and detergents manufacturer is perfecting a production process that can handle a wide variety of raw materials and finished products, while also performing a unique range of loading, unloading, transfer, packaging and filling operations.
The global nature of the industry also creates challenges for manufacturers. Numerous changes in the global supply chain for raw materials, the creation and use of new chemicals, along with expensive fragrances, colorants, preservatives and advanced soap formulations combine to keep manufacturers increasingly ready to react. That is a difficult task, especially considering the complexity of soap and detergents manufacturing.
A typical soap and detergents manufacturing facility that specializes in producing products for all four of the main market segments will handle hundreds of different raw materials during the course of a 24-hour production cycle. These raw materials can include many different types of natural and synthetic feedstocks, such as:
■ Animal fats
■ Vegetable oils
■ Fish oils
■ Fatty acids
■ Brines
■ Tallow
■ Glycerin
■ Alkaline solutions
● Potash
● Caustic Soda
■ Deionized water
■ Surfactants
■ Builders
■ Enzymes
■ Additives
■ Fragrances
■ Brighteners
■ Fillers
The Solution
When it comes to identifying the best pumping technology for use in the complete array of product-handling and transfer operations that occur in soap and detergents manufacture, there is really only one standout choice: positive displacement sliding vane pump technology. For more than a century, sliding vane technology has been setting the standard in reliable, cost-effective and efficient performance in soap and detergents manufacture.
Sliding vane technology delivers a number of crucial benefits to soaps and detergents manufacturers, particularly when compared to the operation of internal gear pump technology in the areas of reliability, product-loss prevention and environmental protection. The sliding vane principle of operation guarantees that a pump’s volumetric consistency will remain constant over the life of the pump. This is not always true for internal gear pumps, which are susceptible to constant wear due to the metal-on-metal design of the pump’s gears, resulting in a reduction in flow capacity. (See Figure 1)
Simply put, sliding vane pumps offer significant performance and life-cycle cost advantages over other pump technologies when used in the soap and detergents manufacturing process. Among these advantages are:
■ Superior Shear-Sensitive Product Handling – the smooth sliding vane action has no metal-to-metal contact, which reduces pump friction, eliminates galling and minimizes the agitation of the liquid while allowing for shear-sensitive handling of fluids and increased pump life
■ Superior Self-Priming and Line-Stripping Capabilities – the sliding vane principle creates unmatched vacuum capabilities that allow lines, tanks and pumps to be cleared of valuable product
■ Superior Volumetric Performance – unlike gear and lobe pumps that lose their volumetric efficiency over time, sliding vane pumps utilize self-adjusting vanes that sustain a pump’s volumetric performance, resulting in productivity gains and energy savings
■ Materials Selection – vane pumps are available with housings of stainless steel or ductile iron and a variety of vane materials that make them compatible with many of the fluids used in soap and detergents manufacturing processes
More specifically, the company that is setting the standard in sliding vane pump design and operation is Blackmer., Grand Rapids, MI, USA, the company whose founder, Robert Blackmer, invented the sliding vane principle more than a century ago. Within Blackmer’s extensive family of sliding vane pumps, the SNP Series Sliding Vane Pump is ideally suited for use in many areas of the soap and detergents manufacturing process.
SNP pumps have been designed with the requirements of soap and detergents manufacturing in mind. They are versatile enough to be used throughout the manufacturing process and perform exceptionally well in the following applications:
■ Top and Bottom Unloading – due to their exceptional vacuum capabilities, SNP pumps allow soap and detergents plant operators to safely unload oleochemical and petrochemical raw materials from railcars, transport trucks and storage tanks faster and more completely than other pump technologies
■ High-Viscosity Product Handling – SNP pumps can handle fluids with viscosities in excess of 20,000 ssu (4,250 cSt) and are also equipped with a removable drain plug that allows self-draining of remaining product
■ Thin-Liquid Product Handling – the SNP’s vane technology ensures superior sealing even after significant in-service time because the pump does not experience any of the efficiency-robbing “slip” that occurs in lobe and gear pumps
Conclusion
The demands placed on soap and detergents manufacturers are various: reliably produce the products on which consumers have grown to rely, be versatile enough to handle new products or formulations, and do all of it in a way that is both environmentally friendly and kind to the company’s bottom line.
These many demands can only be met satisfactorily if the manufacturing process includes pumping equipment that delivers the best in reliability, versatility and efficiency. Therefore, savvy soap and detergents manufacturers are turning to positive displacement sliding vane pump technology to address the challenges that arise in their operations. For more than a century, sliding vane pumps have been the technology of choice for numerous industries, and their wide-ranging benefits continue to make them the ideal choice for the many unique operational processes that characterize the global soap and detergents manufacturing industry.
About The Author
Tom Stone is the PSG Director of Marketing for Blackmer®, based in Grand Rapids, MI, USA. He can be reached at tom.stone@psgdover.com. For more information on Blackmer’s full line of pumps and compressors, please go to blackmer.com or call (616) 241-1611. Blackmer is a member of Dover Corporation’s PSG, Downers Grove, IL, USA, which is comprised of several leading pump companies – All-Flo, Almatec®, Wilden®, Blackmer®, EnviroGear®, Griswold™, Mouvex®, Neptune™, and Wilden®. You can find more information on PSG at pumpsg.com.
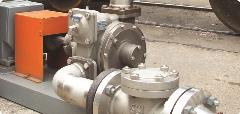
The soap and detergents industry is experiencing significant growth in new products. To keep up with demand, manufacturers must use the best possible equipment – such as product transfer pumps – in all areas of their manufacturing processes.
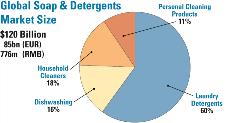
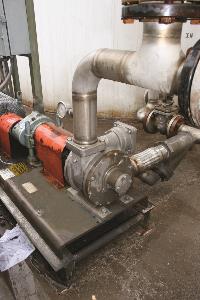
Blackmer SNP Series Sliding Vane Pumps (pictured) are ideal for use in various feedstock transfer applications found in and around soap and detergents manufacturing plants.
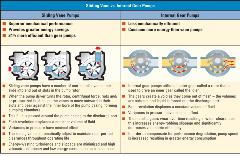
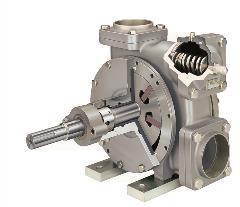
Blackmer SNP Series Sliding Vane Pumps