Rapidly growing Diesel Exhaust Fluid market creates opportunities for pumps that can efficiently operate along the many points of the DEF supply chain
By F. Scott Jackson
Introduction
Growth and innovation in industrial pump design and operation is oftentimes driven by outside forces. One of the more common of these forces is the creation of a new market. A recent example of this as it relates to new opportunities for transfer pumps was the U.S. Environmental Protection Agency’s (EPA) announcement a decade ago that tougher new emission-control standards for all on-road vehicles were to be phased in from 2007-2010. Specifically, all new on-road vehicles must now meet a tailpipe-emission standard of 0.2 grams of nitrogen oxide (NOx) per brake horsepower-hour (g/bhp-hr). This is a huge reduction in the amount of NOx and particulate matter that can be legally emitted into the atmosphere, especially considering that the standard was 5.0 g/bhp-hr in 1994 and still 1.2 g/bhp-hr as recently as 2007.
When the manufacturers of diesel-powered vehicles were looking for ways to make their vehicles compliant with the new emission-control regulations, they turned their gaze to Europe, where similar measures had been in place since the early 1990s. One of the most popular ways to control NOx emissions on European diesel vehicles was through the use of Diesel Exhaust Fluid (DEF), or as it was originally known in Europe, Aqueous Urea Solution 32 (AUS 32), which is a urea-based chemical reactant consisting of 32.5% urea and 67.5% deionized water that is injected into the vehicle’s exhaust stream. The most common process for this injection is called Selective Catalytic Reduction (SCR), where the exhaust is turned into harmless nitrogen and water vapor.
This commitment to DEF – which has been called “the largest addition to the motor-vehicle liquids marketplace in decades” – and its role in the SCR process as the main means for diesel-powered vehicles to meet the EPA’s new emission-control regulations has opened a new market in the United States. Though estimates vary, it’s safe to say that the amount of DEF that will be consumed in the U.S. by the year 2014 will be between 300 million and 600 million gallons annually.
With the advent of this new DEF market comes the creation of a new supply chain, one that must be populated with enough DEF to keep every diesel-powered vehicle on the road compliant with the EPA’s mandate. This white paper will show how advances in DEF-specific pumping technology and its use in critical points along the supply chain will help optimize the availability of DEF to end-users who will rely on it to keep their diesel-powered fleets compliant.
The Challenge
Whenever a new motor-vehicle liquid enters the marketplace, the first responsibility of the companies that will develop equipment designed to produce and handle it is to identify the liquid’s characteristics. DEF has a number of unique characteristics that must be taken into consideration when transporting, storing or using it, including:
• Because of its water content, DEF freezes below 12ºF (-11ºC), meaning it must be protected from extreme cold during storage
• When DEF freezes, it goes from a liquid state directly to a solid with no intermediate “slushiness” stage
• DEF can freeze and thaw with no resulting degradation of the urea solution
• It is stable at storage temperatures up to 84ºF (29ºC); exposing DEF to heat above 90ºF (32ºC) will decrease its useable shelf life
• When exposed to air, the water in DEF will evaporate and produce crystallized urea, which can harm the vehicle’s SCR unit, as well as any transfer or pump components
• DEF cannot become contaminated at any point during its handling; if it does, the SCR system can be compromised, which could lead to such problems as engine failure on the vehicle
With that said, the most important of DEF’s characteristics for pump manufacturers to be aware of is its incompatibility to a number of materials that are commonly used in the automotive-liquid supply chain. Namely, DEF is incompatible with aluminum, bronze, carbon steel, copper, iron, nickel and zinc. On the other hand, stainless steel, polytetrafluoroethylene (PTFE), fluorocarbon and composite plastics like polyethylene or PVC have proven to be compatible with DEF’s corrosive properties.
Another major consideration for the pump manufacturer who is creating equipment for handling DEF is becoming familiar with the points along the supply chain where pumping equipment is necessary. As the DEF market in the U.S. begins to grow and mature, the production-and-supply process, as well as the specific roles that pumps play in it, is becoming more well-defined:
• Tanker trucks and railcars deliver urea and deionzied water to chemical plants where the components are blended together to create DEF
• The newly produced DEF is transported by truck or railcar to a terminal storage location
• At the storage terminal, the DEF is pumped into various types of packages, generally some combination of 330-gallon IBC totes, 55-gallon drums and two-gallon bottles
• These packages are then delivered to retail fueling centers, automotive-product retailers and maintenance-repair shops
• In some cases, DEF is transported via tanker truck to retail fueling sites (most commonly, at this point in the DEF market’s development, large truck stops) where it is transferred into DEF dispensers that are similar to gasoline/diesel pumps and made available for purchase by the public
The Solution
Two crucial pressure points in the supply chain where transfer pumps can help optimize DEF-handling operations are from the production plant to the storage terminal, and when the DEF is transferred at the terminal location into the various types of packaging. To aid the DEF producer, transporter and packager, Blackmer®, Grand Rapids, MI, USA, has created a series of positive displacement sliding vane pumps that not only meet DEF’s product-handling needs, but have also been designed to be materially compatible with its corrosive nature. Additionally, they offer energy-efficient operation that will help keep energy costs under control.
Blackmer also took great pains to ensure that all of its DEF-handling pumps are designed and manufactured to meet ISO standard 22241-3:2008, which is titled “Diesel Engines: NOx reduction agent AUS32.” All of Blackmer’s DEF pumps will meet or exceed that ISO specification, which includes a list of recommended and not recommended materials of construction. The 22241-3:2008 standard also communicates the level of cleanliness that must be attained for wetted surfaces that come in contact with DEF during the transfer process in order to avoid product contamination.
When the DEF is taken from the production plant to the storage terminal, it is generally by either railcar, which can transport anywhere from 10,000 to 15,000 gallons (37,854-56,781 liters) of DEF at a time, or transport truck, which can carry loads ranging from 6,000 to 8,000 gallons (22,713-30,283 liters). At the terminal, the DEF needs to be offloaded quickly, at rates up to 250 gallons per minute (947 liters per minute).
Taking all of those operational demands into consideration, Blackmer has created the STX3-DEF Series Sliding Vane Pump. The 3-inch STX3-DEF pump can deliver flow rates up to 250 gpm at speeds of 800 rpm and differential pressures up to 125 psi (8.6 bar). This means that a 6,000-gallon transport truck can be unloaded in as little as 24 minutes. The pump’s sliding-vane principle of operation also makes it better for these types of operations than, say, centrifugal-pump technology because the design allows it to easily prime and pull a vacuum, which centrifugal pumps have a harder time doing, especially when dealing with piping configurations that have a restricted inlet or long runs. The STX3-DEF pump is also constructed of stainless steel, which makes it highly compatible with DEF.
When considering DEF transfer from storage tanks into IBC totes, drums and jugs, Blackmer developed the STX1220ADEF Series Sliding Vane Pump. The STX1220A-DEF pumps, which have no pushrods, run at speeds up to 1,200 rpm and can deliver flow rates from 49 to 92 gpm (186-348 lpm), which is the “sweet spot” during package-filling operations. Some diesel haulers are also dedicating a storage compartment on their straight delivery trucks for DEF and mounting STX1220A-DEF pumps on them so they can deliver a load of DEF to a fueling site when they are making a fuel delivery. Like their STX3-DEF counterparts, the STX1220A-DEF models are constructed solely of stainless steel, can handle differential pressures up to 125 psi (8.6 bar) and can be used in temperatures up to 240ºF (115ºC).
Blackmer is also finalizing the development of its newest offering for the DEF-handling market – the STX2-DEF Series Sliding Vane Pump. The STX2 is a 2-inch pump that will be similar to the STX1220A, with one notable exception: it is designed with pushrods so that it can run at slower speeds, making it ideal for package-filling operations that require flow rates between 25 and 30 gpm (95-114 lpm). The design of the STX2-DEF pump also means that it can be used with higher-viscosity fluids, which opens it up for use in other non-DEF markets down the road.
All of Blackmer’s STX-DEF pump models can be powered by a base-mounted electric drive, diesel motor, truck-mounted power take-off (PTO) or hydraulic drive, and they are equipped with a double-ended straight-keyed drive shaft that allows either clockwise or counterclockwise rotation.
Conclusion
Though the exact size of the DEF market in the United States in future years is impossible to predict, there’s no question that the EPA’s new emission-control regulations, combined with most diesel-vehicle manufacturers choosing SCR as the best way to satisfy those regulations, leave no doubt that the DEF market will continue to grow. Playing a pivotal role in this growth are the pumps that will be used to deliver raw materials, transfer finished products to storage locations and fill various types of packages for eventual use by the end-user.
Recognizing the potential in this new market, Blackmer has made a commitment to developing the types of pumps that will find a use at all points in the DEF production-and-supply chain. Blackmer has used its more than 100 years of experience in pump manufacture, as well as the tried-and-true qualities of the sliding-vane operating principle, to create a series of transfer pumps that are not only compatible with DEF’s unique characteristics, but able to operate in a fashion that is both energy-efficient and cost-effective for the end-user.
About The Author
F. Scott Jackson is the Product Manager, Americas, for Blackmer®, based in Grand Rapids, MI, USA. He can be reached at scott.jackson@psgdover.com or (616) 248-9218. For more information on Blackmer’s full line of pumps and compressors, please go to blackmer.com or call (616) 241-1611. Blackmer is a member of Dover Corporation’s PSG®, Downers Grove, IL, USA, which is comprised of several leading pump companies— All-Flo, Almatec®, Blackmer®, EnviroGear®, Griswold™, Mouvex®, Neptune™, RedScrew® and Wilden®. You can find more information on PSG at pumpsg.com.
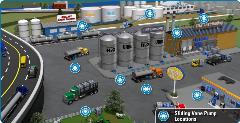
The many loading, unloading and transfer points along the Diesel Exhaust Fluid production and supply chain are ideal for Blackmer’s new DEF sliding vane pumps.
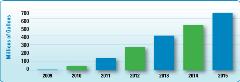
Source: Integer Research, KOST USA, www.DEFendal.com
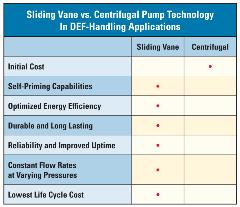
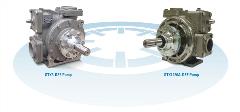
[Sidebar]
What is Selective Catalytic Reduction?
Selective Catalytic Reduction (SCR) was originally developed in Europe as a way to reduce emissions in power plants and utilities. In the 1990s, German automotive giant Daimler AG became the first automotive company to use SCR technology in mobile applications for the control of emissions from light- medium- and heavy-duty diesel vehicles.
In an SCR system, a liquid reducing agent composed of urea and purified water (Diesel Exhaust Fluid) is combined with engine exhaust in the presence of a catalyst to convert NOx into harmless nitrogen and water vapor, which is then introduced into the atmosphere through the vehicle’s tailpipe as part of the normal exhaust process.
The actual SCR process begins when hot diesel exhaust from the engine flows through a diesel particulate filter toward the SCR system. At this point, the DEF is injected into the exhaust stream, which enters into the SCR chamber. In the presence of the SCR catalyst, the exhaust and DEF solution react to convert the NOx into nitrogen and water vapor. This process has been shown to reduce NOx emissions by up to 90%, while lowering particulate emissions by more than 95%.
Since even small amounts of impurities can severely damage the performance of a vehicle’s SCR system, high-purity water must be used in DEF in order to avoid contamination, which will make the DEF in compliance with its ISO 22241 production standards. Impurities in DEF must also be avoided at all points along the supply chain, which necessitates the need for pumping technology that can adequately clear lines, which is one of the main advantages of using sliding vane pumps from Blackmer® in all DEF-handling applications.
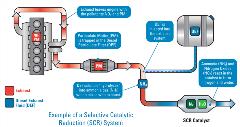