As Utility Costs Rise, Sliding Vane Pump Technology is the Preferred Choice for Energy-Efficient Operation in all Types of Liquid-Storage-Terminal Applications
By Tom Stone
Introduction
As recently as 10 years ago, a liquid storage terminal was considered to be operating at maximum efficiency and profitability if it could turn its tanks once a month. Faced, however, with increasingly razor-thin operating margins, terminal operators began to realize that the more they turn their tanks, the higher rate of return on their investment. Today’s liquid storage terminals are now aiming for a minimum tank turn rate of three to four times per month, with some highly successful operations able to achieve a turn rate of 20 times per month per tank.
These eye-opening – and, until recently, unheard of – turn rates must be combined with operating the terminal at its peak efficiency. It means not only turning the tanks as often as possible, but also doing it in the most energy-efficient manner. This white paper focuses on the many ways that the energy-conscious design and operation of sliding vane pump technology can not only optimize terminal throughput and turn rates, but trim the energy- and profit-wasting fat from the terminal’s bottom line.
Priming The Pump
Liquid storage terminals come in all shapes and sizes, from one- and two-tank bulk plants to sprawling complexes dotted with 50,000-gallon (189,000-liter) storage tanks that are operated by major crude-oil refiners and chemical processors. The commodities that pass through and are stored at liquid terminals also run the gamut: from mainstream and niche chemicals to petroleum products, alternative fuels, vegetable oils, animal fats, LPG and LNG, to name a few.
While the size of a liquid terminal and the products that it handles can vary widely, all of them – in order to operate at the throughput rates demanded – are heavy energy consumers. That high energy usage, coupled with consistently rising energy prices, creates a potentially profit-robbing threat to all terminal operators, regardless of size.
Among the biggest consumers of energy at a liquid storage terminal are the transfer pumps that play a key role in the terminal’s supply chain. In fact, studies have shown that pumps account for nearly 27% of total electricity use in the industrial sector.
Because of that, it’s safe to say that no matter the size of the facility or the commodities being handled, a terminal’s operation would falter with unreliable transfer pumps. Pumps are used to unload the barges, railcars and trucks that bring raw materials to the terminal, and transfer those materials to storage tanks. They are also used to transload materials from one mode of transportation to another, and into transport vessels for delivery to the end-user.
This reliance on pumps, coupled with their high energy usage, can create a Catch-22 for the operator. Throughputs must be maintained and maximized, but now they must be done in the most energy-efficient manner possible. To combat this, terminal operators around the globe are beginning to implement energy-management processes and procedures that are designed to:
■ Drive throughput improvements that can increase financial performance
■ Control energy expenses by reducing power consumption without compromising throughput performance, or even increasing throughput levels
■ Increase operational reliability and process integrity by emphasizing the use of energy-efficient technologies that support enhanced mechanical efficiency
■ Reduce vulnerability to energy-price volatility
In many cases, the implementation of sliding vane pump technology provides the ultimate solution in meeting these new energy-efficiency imperatives.
A Systems Approach
More and more terminal operators are becoming aware that taking a systems approach is the best way to significantly improve the overall energy efficiency of their facilities. In a systems approach, operators strive to improve the reliability, performance and efficiency of their overall pumping system, which will result in greater energy savings and enhanced productivity and profitability.
The foundation of a successful systems approach is identifying and then implementing the best pumping technology in a system setup that is properly sized and has an appropriate piping design, control-valve configuration and motors to ensure the highest operational efficiency. There is a specific “best use” for all pumping technologies. Understanding how energy-efficiency is measured and affected by the type of pump being used and the overall system configuration is vital to creating an energy-optimized pumping system.
To aid in this process, the use of Life Cycle Cost (LCC) analysis allows the terminal operator to compare operations, maintenance and energy consumption costs between different pump technologies that could be used for the same application. LCC can identify the total cost of ownership, from initial equipment costs, installation costs, energy costs, maintenance/repair costs and downtime costs to a final decommissioning cost. Used wisely, an LCC analysis will dramatically reduce waste and deliver maximum efficiency.
For instance, a positive displacement sliding vane pump may have a higher initial cost than a centrifugal pump. However, over the life span of the respective pumps, the use of a centrifugal pump will, on average, result in higher operating, energy, maintenance, downtime and environmental costs that are incurred by the facility operator when compared to the pump that operates via sliding vane technology.
The Centrifugal Conundrum
Centrifugal pump technology is the most common technology for many industrial and terminal operations, with some estimates indicating that centrifugals are used in 75% of industrial process-pump applications. However, is centrifugal-pump technology the best or most energy-efficient choice in terminal applications? The answer, after examining the evidence, in many applications is “No.”
The sweet spot in a centrifugal pump’s operation is what is known as the Best Efficiency Point (BEP). When operating at its BEP, a centrifugal pump is working at its highest point of efficiency.
Unfortunately, centrifugal pumps very rarely operate directly on the BEP because ideal pumping conditions are hard to fabricate. Still, the design of centrifugal pumps allows them to function as they move away from the BEP, generally within 80% to 110% of the BEP, though the farther removed from the BEP, the less efficient the operation.
It’s when the operation of the pump is removed from the BEP that bad things will begin to happen. Most critical is that there will be uneven pressure on the impeller, which will result in increased radial thrust that causes the pump shaft to deflect. When shaft deflection occurs there will be excess load on the radial bearings and excess deflection of the mechanical seal. Operating too far outside of the BEP can also lead to cavitation. This cavitation, essentially the formation and implosion of bubbles within the liquid during the pumping process, can destroy the pump – and, possibly, other system components - in a short period of time.
In addition to the harm that can result when operating too far off the BEP, there are other drawbacks to the use of centrifugal pumps in liquid-terminal operations. Among them:
■ Due to pump-selection complexity, over-sized pumps are often chosen, resulting in increased operating and maintenance costs, inefficient operation, increased chance of cavitation and higher-than-necessary energy consumption
■ As pump differential pressure increases, the flow rate decreases. Low-flow centrifugal pumps consume more energy and require more pressure, which is costly
■ The performance of a centrifugal pump will be adversely affected if pumping a fluid that has a viscosity higher than 400 cSt
The Sliding Vane Solution
As liquid-terminal operators look for ways to maximize not only the throughput but also the energy-efficiency of their facilities, many are replacing their centrifugal pumps with positive displacement sliding vane pumps from Blackmer®, Grand Rapids, MI, USA. For more than 100 years, Blackmer has been a leading global provider of sliding vane pump technology for the transfer of liquids and gases. The energy- and mechanically efficient design of Blackmer sliding vane pumps allow them to offer terminal operators high-value advantages in their effort to implement energy-saving initiatives.
Because of their energy-friendly operational ability, Blackmer has made its sliding vane technology a main component of its Smart Energy® Flow Solutions program. Blackmer Smart Energy products are designed to enable pump users to gain a competitive business advantage through the deployment of energy-saving positive displacement sliding vane pump technology.
The energy-saving features and benefits that sliding vane pump technology can provide in liquid-terminal transfer applications are myriad:
■ Ability to handle both very-thin liquids (gasoline, ammonia, LPG, solvents, etc.) and those with viscosities up to 50,000 cSt
■ Flow rates up to 2,000 gallons per minute (7,580 liters per minute)
■ Flow rates directly proportional to the pump’s speed
■ Effectively generate high pressure in low-flow applications
■ Lower overall cost of ownership when compared to centrifugal pumps
■ Rotary design minimizes energy-robbing pulsation
■ Dry-run and self-priming capabilities
■ Excellent suction lift and line-stripping capabilities
■ High volumetric efficiency due to self-adjusting vanes that eliminate energy-robbing slip
Conclusion
The current-day demands that are put on liquid-storage terminals can appear to be at cross-purposes: maximize turn rates and throughputs while minimizing energy consumption. While this balancing act may be daunting, there is a readily available solution for terminal operators.
That solution is the incorporation, where applicable, of positive displacement sliding vane pump technology into the terminal’s pumping system. For more than 100 years, sliding vane pumps have been designed to provide streamlined, reliable operation while consuming low amounts of energy, especially when compared to the efficiency and energy-consuming drawbacks that are characteristic of centrifugal pump operation.
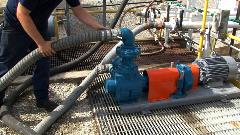
Demands put on liquid-storage terminals appear to be at cross-purposes: maximize throughput while minimizing energy consumption. Nevertheless, sliding vane pumps provide a transfer technology that offer streamlined, reliable operation while consuming low amounts of energy.
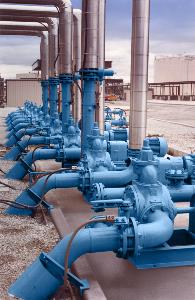
The energy- and mechanically-efficient design of Blackmer sliding vane pumps allow them to offer terminal operators advantages in energy-saving initiatives.
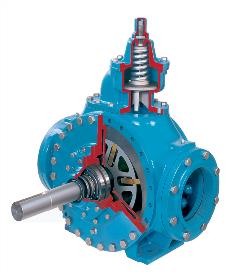
Blackmer® HXL Series Sliding Vane Pumps
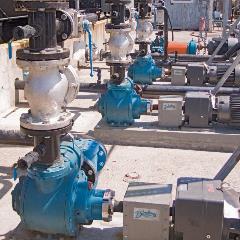