Twenty-seven percent of electricity consumed in an industrial system is used to operate pumps. Using Blackmer® Smart Energy® Sliding Vane Pumps in your operation can cut these costs.
By Thomas L. Stone
Introduction
Manufacturers of oils, surfactants, detergents and related materials must not only meet strict production quotas, but they must ensure that the products meet the needs and expectations of the consumer. In recent years, two new variables have been introduced to the oils, surfactants, detergents and related materials manufacturing equation. As energy costs continue to rise, pressure is being put on the manufacturer to control those costs through the implementation of pumping systems that are more bottom-line friendly. At the same time, plant operators are being asked to make a commitment to having their operations be more “green” or “sustainable,” meaning the introduction of a variety of operational enhancements that are deemed to be more environmentally friendly. These new areas of emphasis will not only make the pumping system more cost-effective, but it will also have less of an impact on the environment in the form of reduced consumption of such energy-producing commodities as coal and petroleum products, as well as a decrease in the amount of exhaust emissions that a plant produces.
The new challenge, then, for the soap and detergents manufacturer is not only to meet or exceed production and quality thresholds, but to do it in the most energy-efficient and environmentally conscious manner possible.
The Challenge
Research conducted by The Hydraulic Institute (HI), and presented in Improving Pumping System Performance: A Sourcebook for Industry, has determined that more than one-quarter of the electricity consumed in an industrial system – 27% to be exact – is used to operate pumps. This makes pumping systems a natural target when identifying ways to reduce energy consumption.
To that end, HI has created a video training program designed to help the viewer identify ways to achieve energy savings. Among HI’s energy-saving suggestions are:
• Design systems with lower capacity and total head requirements. Reducing flow capacity through the use of lower velocity in the heat exchanger and the elimination of open bypass lines will lower energy consumption, as will a reduction in total head requirements through a decrease in pressure and elevation changes, along with the use of larger pipes and low-loss fittings.
• Don’t allow for an excessive margin of error in capacity or total head. Energy savings can be as high as 20% if pumps are sized based on reasonable system head and capacity requirements.
• Select the most efficient pump type and size from the onset. Ultimately, the choice of pump depends on the service needed from the pump. However, consideration must also be to flow, pump speed, inlet pressure and net positive suction head, as well as the type of liquid to be pumped. Selecting the proper pump for the job at the start – rather than emphasizing initial cost – will result in additional energy savings in the long run.
• Use two or more smaller pumps instead of one larger pump to optimize capacity. Two pumps can be operated in parallel during peak demand periods with one pump operating by itself during periods of lower demand. In this setup, energy savings results from running each pump at a more efficient operating point while avoiding the need to throttle back a larger pump during low-demand periods.
• Maintain pumps and components in virtually new condition. Simply put, wear is a significant cause of decreased pump efficiency. To avoid excessive wear, pump bearings must be properly lubricated and replaced before they fail. Shaft seals also require constant maintenance to avoid premature mechanical failure. In the end, properly maintaining pumps will not only optimize the quality of the products that they are charged with producing, but will also maximize energy usage.
In addition to these suggestions, HI also suggests that a life-cycle cost analysis be performed before a pumping system is installed. Too often, plant operators are concerned only with front-end costs, not realizing that the total life-cycle cost of a pumping system can escalate precipitously if inefficient or unreliable pumps and components are used. Determining the total life-cycle cost of a pumping system may mean a higher outlay in the beginning, but it could deliver a series of money-saving advantages through the complete lifetime of the pump.
The Solution
Blackmer®, Grand Rapids, MI, USA, a leading global provider of positive displacement sliding vane pumps for use in industrial applications, and a member of the Dover Corporation’s PSG®, Oakbrook Terrace, IL, USA, is well aware of the new energy and environmental challenges now facing manufacturers of oils, surfactants, detergents and related materials.
Blackmer has made its sliding vane pump technology, which was perfected by company founder Robert Blackmer in 1899, a foundation of its Smart Energy® Flow Solutions program. With worldwide industrial energy consumption expected to increase by 42% through the year 2035, Blackmer has designed its Smart Energy products to help manufacturers of oils, surfactants, detergents and related materials gain a competitive edge through the deployment of energy-saving sliding vane pump technology.
Of the leading positive displacement pump technologies, sliding vane pumps are the most energy-efficient, thanks to a series of design features that give them an edge in mechanical efficiency over, for example, gear and lobe pumps. Most significantly, the self-adjusting vane design of Blackmer sliding vane pumps eliminates energy-robbing product “slip” and promotes high volumetric consistency even after substantial in-service time. Side-by-side comparisons show that sliding vane pumps can be as much as 24% more efficient than gear models.
Conclusion
The demands placed on manufacturers are strict and diverse: reliably produce the products that consumers demand while at the same time doing so in the most cost-effective and environmentally friendly manner possible. These demands can only be met if the pumping equipment utilized in the manufacturing process is versatile enough to simultaneously deliver the best in product quality and bottom line-compatible operation.
Blackmer has recognized these challenges and made a commitment to energy and environmental efficiency with its Smart Energy® Flow Solutions program.
About The Author
Thomas L. Stone is the PSG® Director of Marketing for Blackmer®, based in Grand Rapids, MI, USA. He can be reached at tom.stone@psgdover.com or (616) 248-9252. For more information on Blackmer’s full line of pumps and compressors, please go to blackmer.com, or call (616) 241-1611. Blackmer is a member of Dover Corporation’s Pump Solutions Group (PSG®), Oakbrook Terrace, IL, USA, which is comprised of several leading pump companies – Abaque™, All-Flo, Almatec®, Blackmer®, EnviroGear®, Griswold™, Mouvex®, Neptune™, Quattroflow™, RedScrew® and Wilden®. You can find more information on PSG at psgdover.com.
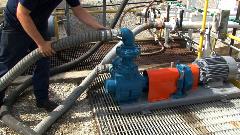
The large amount of energy that is consumed in a manufacturing operation requires the right type of pump in order to optimize energy costs. The operation of Blackmer® Smart Energy® Sliding Vane Pumps provides the solution in a wide range of oils, surfactants and detergents manufacturing applications.
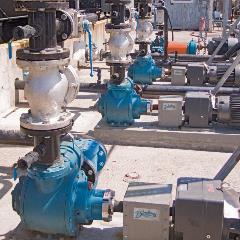
Blackmer® Smart Energy® Sliding Vane Pumps can be a critical energy-conscious component in a soap and detergents manufacturing operation.
[Sidebar]
Blackmer® SNP Series Sliding Vane Pumps
Recognizing the diverse pumping requirements in soap and detergents manufacturing, Blackmer® offers the SNP Series Sliding Vane Pump. The SNP pumps have been designed with cost-effectiveness and environmental sustainability in mind, and offer the following features to soap and detergents manufacturers:
• Superior top and bottom unloading capabilities, thanks to exceptional lift, line-stripping and tank-clearing characteristics
• The ability to handle liquids with viscosities as high as 4,200 cP, while also being equipped with a removable drain plug for complete self-draining
• Unmatched thin-liquid pumping that is the result of superior sealing even after significant in-service time
• Sustained performance that is guaranteed by the SNP’s unique self-adjusting sliding vane principle of operation
All of these features make Blackmer’s SNP Series pumps ideal for energy-efficient use throughout the soap and detergents production chain, from raw material unloading and transfer to the packaging of liquid detergents and soaps. Since they are available in stainless-steel and ductile-iron construction, SNP pumps can handle the full spectrum of fluids used in soap and detergents production, from caustic fluids such as fatty acids, brines and alkalis, to surfactants, glycerins, tallow, vegetable oils, sodium hydroxide, builders and additives.
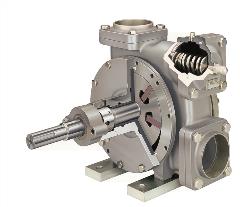
Blackmer® SNP Series Sliding Vane Pump
[Sidebar]
Related Markets…One Pump Solution
Industries do not operate in a vacuum. One industry’s waste product may be another’s feedstock. For example, take the manufacture of two seemingly unrelated products – soap and detergents, and biodiesel that is used to power motor vehicles.
As the production and use of biodiesel has grown so has the world’s supply of crude glycerin, which is a by-product of the transesterification process within biodiesel production. In fact, beginning in 2006 and continuing through 2015, the United States biodiesel industry is expected to produce 1.4 billion pounds of glycerin. This glut of crude glycerin has forced prices for the commodity down, meaning that many biodiesel producers are selling their excess glycerin at a loss.
As it happens, crude glycerin that is filtered to remove any food particles or impurities can be made into bar soap. Bar soap made from glycerin has excellent degreasing abilities, making it ideal for cleaning applications that require the breakdown and removal of greases and oils. Additionally, by adding various fragrances and dyes, glycerin can be used to make household soap, as well.
While the features of Blackmer® SNP Series Sliding Vane Pumps make them highly effective in the production of soap and detergents, their stainless-steel construction, metalized-carbon sleeve bearings and non-metallic vanes also give them the ability to handle the caustic fluids that are used in the biodiesel production process. The wetted parts of SNP pumps are also non-galling, which reduces maintenance worries and costs.
So while two industries may appear to have nothing in common, oftentimes they do – and in the case of soap and detergents and biodiesel production, one of those commonalities is the ability of SNP Series Sliding Vane Pumps from Blackmer to meet the liquid-handling and transfer needs of the respective manufacturing facility operator.
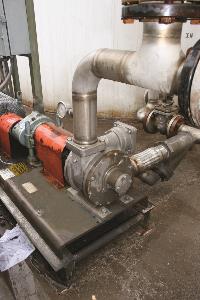
Blackmer® SNP Series Sliding Vane Pumps offer operational advantages for two seemingly unrelated industries-the manufacture of biodiesel and soap and detergents-with waste elements from the first able to be used to create end-products for the second.