A SURGE IN THE NUMBER OF STORAGE TERMINALS IN THE MIDDLE EAST AND NORTH AFRICA HAS POSITIONED SLIDING VANE PUMPS AS THE BEST CHOICE FOR ENERGY-EFFICIENT PUMPING TECHNOLOGIES
By Thomas L. Stone
Introduction
Since its formation in 1960, the Organization of Petroleum Exporting Countries, better known as OPEC, has been the undoubted dominant global force in the production of crude oil. Despite recent gains in production in the United States, daily production by the 12 current members of OPEC stood at 30.5 million barrels per day (b/d) in December 2014; by comparison, U.S. daily production was 9.2 million b/d in January 2015. Additionally, it is estimated that OPEC’s members produce about 40% of the crude oil that the world consumes daily.
With eight of the OPEC countries—Iran, Iraq, Kuwait, Qatar, Saudi Arabia, United Arab Emirates, Algeria and Libya—located in either the Middle East or North Africa (and known as MENA countries), it stands to reason that the region is also home to one of the world’s most sophisticated refined-petroleum products storage-terminal networks. While that is the case, it is also true that the MENA storage-terminal market is ripe for significant investment and expansion.
According to easyFairs, a Brussels, Belgium-based trade-event organizer that helped launch the inaugural Tank Storage Middle East conference and exhibition from Jan. 26-27, 2015, at the National Exhibition Centre in Abu Dhabi, United Arab Emirates, “the Middle East is a critical growth area for the storage-terminal industry, with more than 40 million m3 (10.5 billion gallons) of independent tank storage in the region.”
In fact, the UAE itself has plans to double its tank capacity over the coming years and its Port of Fujairah, a multi-purpose port on the Eastern seaboard of the UAE located 97 kilometers (60 miles) from the Straits of Hormuz, recently expanded its storage capacity to 8.67 million m3 (2.3 billion gallons) with plans to expand to around 12 million m3 (3.2 billion gallons) by 2017. This will give Fujairah the world’s second-largest bunkering capacity behind Singapore’s Jurong Island facility.
Non-OPEC Oman, the UAE’s next-door neighbor on the Gulf of Oman, is also focusing on expansion of its storage-terminal industry. According to a January 2015 article titled “Fuel Bunkering in Oman: Behind the Scenes,” which was penned by Edwin Lammers, a presenter at Tank Storage Middle East, “millions of dollars are being injected into new bunkering infrastructure and pipelines” in Oman.
A similar story is being told in the countries of North Africa, with the region’s growth in tank-terminal construction being driven by increased stability, expanding demand, booming populations and significant discoveries of recoverable crude oil. Horizon Terminals, a subsidiary of Emirates National Oil Company, recently opened a new storage facility in Tangiers, Morocco, while other North African nations (Libya, Algeria, etc.) have new storage-terminal plans on the drawing board.
This growth in terminal sites and overall storage capacity in the MENA region also increases the demand for pumping equipment that can adequately meet the requirements of handling refined-fuel products. This article will illustrate how the design and operation of sliding vane pump technology can most efficiently optimize throughput rates at refined-petroleum products storage-terminal facilities.
The Challenge
With millions of gallons of refined-petroleum products needing to pass through MENA-based storage facilities on a daily basis, terminal operators must employ a battalion of transfer pumps. These pumps must not only operate reliably and at pre-determined flow rates, but must do so cost-effectively. With some pumping technologies—centrifugal, gear and lobe, for example—this is often easier said than done.
The biggest consumers of energy at a storage terminal are often the transfer pumps that play a key role in the terminal’s supply chain. In fact, studies have shown that pumps can account for up to 30% of the total electricity use in the industrial sector, while the average efficiency level of a pumping system is generally 40% or less. This means that when pumping systems are not optimized to perform at the highest level of efficiency, they will adversely affect the facility’s profitability due to higher energy and maintenance costs, shorter mean time between repairs and compromised reliability.
This reliance on pumps, coupled with their high energy usage, can create a difficult situation for the operator. Throughputs must be maintained and maximized, but they must be done in the most energy-efficient manner possible. To combat this, terminal operators around the globe are beginning to implement energy-management processes and procedures that are designed to:
• Drive throughput improvements that can increase financial performance
• Control energy expenses by reducing power consumption without compromising overall throughput, or even increasing throughput levels
• Increase operational reliability and process integrity by emphasizing the use of energy-efficient technologies that support enhanced mechanical efficiency
• Reduce vulnerability to energy-price volatility
That being said, too many terminal operators are still reflexively turning to centrifugal-style pumps for their product-handling needs, which may not be the best or most energy-efficient choice for terminal applications. The sweet spot in a centrifugal pump’s operation is known as the Best Efficiency Point (BEP). When operating at its BEP, a centrifugal pump is not only working at its highest point of efficiency, but is also at the point where the product flow rate and discharge pressure are equal around the pump’s impeller and volute.
Unfortunately, centrifugal pumps very rarely operate at their BEP because ideal pumping conditions are hard to replicate, and the farther removed from the BEP, the less efficient the operation.
It’s when the operation of the pump is too far removed from the BEP that performance will begin to be compromised. Most significantly, there will be uneven pressure on the impeller, which will result in increased radial thrust that will cause the pump shaft to deflect.
When shaft deflection occurs there will be excess load on the bearings and excess deflection of the mechanical seal, as well as the potential for uneven wearing of the shaft sleeve. Operating too far outside of the BEP can also lead to cavitation of the pumped medium. This cavitation, essentially the formation and collapse of bubbles within the liquid during the pumping process, can destroy the pump and, potentially, the surrounding system in a short period of time.
In addition to the harm that can result when operating too far off the BEP, there are other drawbacks to the use of centrifugal pumps in liquid-terminal operations. Among them:
• Over-sized pumps are often chosen, resulting in increased operating and maintenance costs, inefficient operation, increased chance of cavitation and higher-than-necessary energy consumption
• As pump differential pressure increases, the flow rate decreases. Low-flow centrifugal pumps consume more energy and require more pressure, which is costly
• Higher flow rates create higher flow velocities, which can lead to friction loss and higher energy consumption
• Centrifugal pump performance will be adversely affected when pumping a fluid that has a viscosity higher than 400 cSt
The Solution
More and more terminal operators are becoming aware that taking a systems approach is the best way to significantly improve the overall energy efficiency of their facilities. In a systems approach, operators strive to improve the reliability, performance and efficiency of their overall pumping system, which will result in greater energy savings and enhanced productivity and profitability.
Therefore, liquid-terminal operators that are looking to maximize the throughput and energy-efficiency of their facilities have a best-in-class choice to replace their centrifugal pumps in the form of positive displacement sliding vane pumps from Blackmer®, Grand Rapids, MI, USA, a global brand of PSG®, a Dover company. Since 1903, Blackmer has been a leading global provider of sliding vane pump technology for the transfer of liquids and gases. The energy-efficient design of Blackmer sliding vane pumps allow them to offer terminal operators high-value advantages in an effort to meet their energy-saving initiatives.
Because of this energy-friendly operational ability, Blackmer has made its sliding vane technology a main component of its Smart Energy® Flow Solutions program. Blackmer Smart Energy products are designed to help pump users gain a competitive business advantage through the deployment of energy-saving positive displacement sliding vane pump technology.
The energy-saving features and benefits that sliding vane pump technology can provide in liquid-terminal transfer applications are myriad:
• Ability to handle both very thin liquids and those with viscosities up to 50,000 cSt
• Flow rates up to 7,850 liters per minute (2,000 gallons per minute)
• Flow rates directly proportional to the pump’s speed
• Effective generation of high pressure in low-flow applications
• Lower overall cost of ownership when compared to centrifugal pumps
• Dry-run and self-priming capabilities
• Excellent suction-lift and line-stripping capabilities
• High volumetric efficiency due to self-adjusting vanes that eliminate energy-robbing slip
Most importantly, while an average terminal facility may spend USD $1.4 million annually on energy to run their pumping systems, better system design and the use of Smart Energy sliding vane pumps from Blackmer can help produce savings that could average USD $350,000 per year in energy alone.
Conclusion
With the ongoing growth in the number, size and volumes handled by MENA refined-product storage facilities, operators must make every effort to optimize the energy efficiency of their operations. With worldwide industrial-energy consumption expected to increase by 42% over the next quarter-century, Blackmer Smart Energy Flow Solutions can help terminal companies control energy expenses by reducing power consumption without compromising performance; increasing operational reliability with energy-efficient technologies that support improved mechanical efficiency; reducing exposure to energy-price volatility; and driving productivity improvements that increase financial performance.
About the Author:
Thomas L. Stone is Director of Marketing for Blackmer® and PSG®. He can be reached at +1 616-241-1611 or Tom.Stone@psgdover.com. Blackmer is a leading brand of rotary vane and centrifugal pump and reciprocating compressor technologies from PSG®, a Dover company. Headquartered in Oakbrook Terrace, IL, USA, PSG is comprised of several leading pump brands, including Abaque®, All-Flo, Almatec®, Blackmer®, Ebsray®, Griswold™, Mouvex®, Neptune™, Quattroflow™, RedScrew™ and Wilden®. For more information on Blackmer or PSG, please go to blackmer.com or psgdover.com.
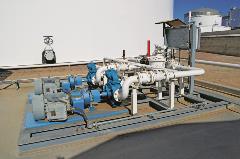
The Middle East and North Africa (MENA) region is in the midst of a construction boom for storage terminals that handle refined petroleum products. To optimize energy consumption at these facilities, which can transfer millions of gallons of petroleum products daily, operators are turning to Smart Energy® Flow Solutions from Blackmer®.
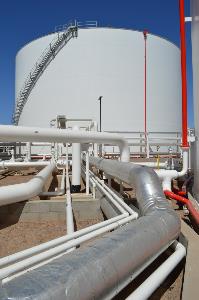
The average efficiency of a typical pumping system is 40% or less. When a storage terminal is moving millions of gallons of refined petroleum products a day, improving efficiency levels is of paramount importance and significant savings can be realized through the utilization of Blackmer® Smart Energy® Flow Solutions.
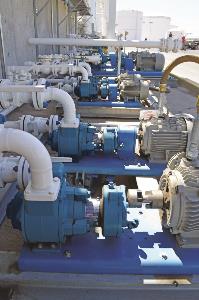
More storage-terminal operators are taking a systems approach to improving the energy efficiency of their facilities and many are realizing that Blackmer® Sliding Vane Pumps can be an important component in an optimized fluid-handling system.
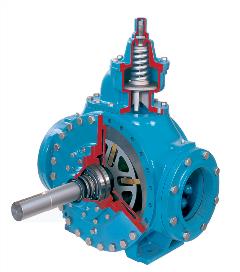
Blackmer® HXL Series Sliding Vane Pump