WENNER GAS AND CHS, INC., DOUBLE CAPACITY AND THROUGHPUT AT ROCKVILLE PROPANE TERMINAL WITH THE AID OF BLACKMER® LB601 SERIES COMPRESSORS AND LGL4 SERIES SLIDING VANE PUMPS
By Bill Holmes
Quick Facts
- Company: Rockville Propane Terminal (formerly Wenner Gas Terminal)
- Location: Rockville, MN, USA
- Market: Propane Storage and Distribution
- Distributor/Design Engineers: LPG & NH3 Supply, Inc., Buffalo, MN, USA
- General Contractor: Alpha Development & Construction LLC; Reggie Fraley, CEO and Development Consultant; (320) 260-4226
- Challenge: Incorporate compressor and pump technologies that would optimize railcar deliveries and loading of propane transports at rapidly expanding propane terminal
- Solution: Blackmer® LB601 Series Reciprocating Gas Compressors; Blackmer® LGL4 Series Sliding Vane Pumps
“I thought it was a pipe dream,” Jeff Munzel, Vice President of LPG & NH3 Supply, Inc., in January 2012.
That so-called pipe dream—the decision by Minnesota’s Wenner family to finance and construct, in 2009 during the height of a brutal economic recession, the new 300,000-gallon Wenner Gas Terminal—has turned into a textbook example of how foresight, hard work and the willingness to take a calculated risk can turn into the American Dream.
“Originally when we built it everybody thought we were crazy, that there was no way we could do enough gallons to be profitable,” recalled Pat Wenner, President of what is now known as the Rockville Propane Terminal. “We started way ahead of what people thought we could do, maybe six million gallons, and we started at 12 million gallons a year. Last year, we did 35 million gallons and we may do as much as 50 million gallons this year.”
With A Little Help From Their Friends
A series of significant shifts in the propane-supply and-distribution market in Minnesota—and Jim, Pat and Carl Wenner’s ability to recognize them and put a plan in place to take advantage of the changes—has been the driving force for the Rockville Propane Terminal from Day One. Since the 1940s, the Wenner family had been supplying propane from a storage facility along state Rt. 23 near its hometown of Cold Spring, MN, USA.
However, when the Wenners learned that the rail spur that ran through Cold Spring would be decommissioned they purchased a six-acre parcel of property up Rt. 23 in Rockville and built the Wenner Gas Terminal, which opened for business in January of 2011. The new facility featured five railcar-unloading positions along a newly built railroad spur with eight propane-storage tanks with a combined storage capacity of 300,000 gallons. There was also an island built where propane transports could be loaded for deliveries. In all, the facility was outfitted with five reciprocating gas compressors and two sliding vane pumps to meet the LPG-transfer requirements.
The next major occurrence in the history of the Rockville Propane Terminal took place in May 2012 when Kinder Morgan Pipeline Energy Partners, L.P., announced that as of July 2014 it would be reversing the flow on its Cochin pipeline, which stretches 1,900 miles from Alberta, Canada, through seven U.S. states and into Ontario, Canada. Instead of carrying propane from west to east, the flow would be reversed and light condensates would be shipped from Kankakee County, IL, USA, to the oil-sands region of Alberta.
This meant that new sources of propane supply would need to identified and cultivated in Minnesota and the Upper Midwest. Seeing the opportunity for expansion, Wenner was ready to take the leap.
“With the pipeline going down, it was a big leap for us to go from being a backup standby terminal to one that is the main choice in the area, but we knew that rail would have to play a bigger role in the state’s propane-supply chain and the opportunity was too good to pass up,” said Wenner.
To make the expansion a reality, though, Wenner needed some assistance. It found it in the form of CHS, Inc., Inver Grove Heights, MN, USA. CHS is the nation’s largest farmer-owned cooperative and the fifth-largest retailer of propane in the United States. It has access to propane supply at 150 terminals in 40 states and five Canadian provinces, along with the largest fleet of pressurized propane-transport vehicles in the country.
“When we wanted to expand, a lot of the banks didn’t think the idea to expand so fast was good, so we ran into a couple of issues,” explained Wenner. “When we went to CHS, all those issues went away. They’ve been a very good partner.”
In November of 2013, CHS announced that it had signed an agreement to create a limited liability company with Wenner Gas Co., as a way to enhance storage and service capabilities at Wenner’s nearly three-year-old propane terminal, which would be renamed the Rockville Propane Terminal. CHS acknowledged that the agreement was just one in a series of actions designed to secure a reliable supply of propane for customers who would be affected by the impending Cochin pipeline reversal.
“The two of us knew each other quite well and what we saw was an opportunity to grow the terminal and grow our market share through that asset,” said Matt Kumm, Propane Marketing Manager for CHS, Inc. “We formed a partnership at that point in time and it has been extremely successful. The terminal is now open 24/7 and has the capability to serve all of our needs as it gets even busier. Wenner Gas started down this road by putting in quality, high-performance equipment and we built upon that model to handle the additional demand.”
With the aid of Reggie Fraley, CEO and Development Consultant for Alpha Development & Construction LLC, Cold Spring, MN, the expansion of the Rockville Propane Terminal moved at warp speed. By September 2014, five additional rail loading towers had been constructed and eight more storage tanks had been added, giving the facility a total storage capacity of 620,000 gallons of propane. A second loading island was also built, meaning the facility could double the number of transports that could be loaded in any given day.
“Reggie Fraley helped us with the financing of the original terminal, got all of the permitting to get the terminal up and running, which was tricky because it’s located in a wetland and we needed wetland mitigation, had to work with county boards, watershed districts, all the environmental issues,” said Wenner. “He helped us get through them and size the plant correctly—and get done on time. From the time we started the terminal until now, we’ve never had any downtime, people could still come through and get their product.”
The Common Denominator
One constant in the growth of the Rockville Propane Terminal has been Wenner’s use and reliance on compressor and pump technologies from Blackmer®, Grand Rapids, MI, USA, a product brand of PSG®, Oakbrook Terrace, IL, USA, a Dover company. When it first opened, the terminal featured five Blackmer LB601 Series Reciprocating Gas Compressors at the railcar-unloading docks and two Blackmer LGL4 Series Sliding Vane Pumps at the dual-transport loading island. Working with railcars possessing a typical capacity of 33,000 gallons, the terminal can now bring in upwards of 330,000 gallons every six or seven hours, or more than one million gallons over a full day.
“We took what was existing at the Wenner terminal and basically doubled it—storage capacity, unloading capacity, number of towers and put in a second loading island,” said Scott McClelland, Engineer at LPG & NH3 Supply, which has supplied the terminal with all of its compressor and pump equipment. “We added one new compressor for each new rail tower, so there are 10 LB601 compressors at the facility, and we added two LGL4 pumps at the new loading island.”
The LB601 compressors are ideal for the terminal’s LPG railcar-unloading operations because they offer an oil-free design with the unique ability to do both liquid transfer and vapor recovery after the tank is emptied. They feature ductile-iron construction that makes them stronger and more resistant to thermal shock and corrosion than cast iron, and leak-free operation that is ensured by the presence of O-rings, instead of gaskets, on all of the pressure-containing parts.
“The Blackmer compressors run fantastic,” said Wenner. “From the time they turn on at 6:00 a.m. until we’re done with what we need to do for the day, they never stop. Some terminals may have bigger compressors, but with the Blackmers we can move the volume we need.”
The four-inch LGL4 pumps have been designed for maximum performance and reliability under the most severe operating conditions. Standard features include cavitation suppression liners that reduce noise, vibration and wear; replaceable casing liners and end discs; ductile-iron construction with internal relief valves; self-priming and dry-run capabilities; and vanes that can be replaced without removing the pump from the piping system, which eliminates maintenance concerns and costly downtime.
Both the LB601 compressors and LGL4 pumps have been able to keep up with the unloading and loading rates that are required—and Wenner is confident they will continue to perform as expected as the terminal continues to increase its throughput rates. However, in the unlikely event that there is any interruption in the operation of the compressors and pumps, Blackmer offers the industry’s longest warranty, 36 months, as well as a one-year Performance Assurance Guarantee that provides free replacement parts during the first 12 months of operation.
“With the 10 Blackmer compressors, we can unload 15 railcars every six or seven hours, and with the four loading pumps, we can do two transports every 15 to 20 minutes,” he said. “We have done as many as 30 to 40 cars per day into the terminal, up to one million gallons into the terminal, and we can do even more. The terminal can move 100 million gallons a year, if we get to the point where we need to move that much volume.”
Conclusion
By definition, a pipe dream is “an unattainable or fanciful hope or dream.” For the Wenners, CHS and Minnesota’s propane-supply network, what was once considered a pipe dream has manifested itself into an undeniable American success story. And riding shotgun in the success of the Rockville Propane Terminal have been Blackmer LB601 Reciprocating Gas Compressors and LGL4 Sliding Vane Pumps.
“Since we opened this facility, we have always been able to take the railcars and unload them fast enough,” said Wenner. “We have never run out of gas so when people want it they can come in and get it; even when other people have had shortages we have never run out. We have never had waits in line either and some terminals can have 20- to 24-hour waits. Now that everything’s set and completed and we’re loading two transports at a time, I don’t ever see us having any waits. That speaks volumes for the Blackmer compressors and pumps; they’re configured correctly, they’re sized correctly and they run efficiently. When you hit a spike and you need to do a million gallons a day back-to-back, we’ve proven we can do it, and that shows that the Blackmer compressors and pumps are reliable.”
About the Author:
Bill Holmes is Director of Sales North America – Energy & Transfer Group for PSG®, Oakbrook Terrace, IL, USA. He can be reached at (847) 726-7565 or Bill.Holmes@psgdover.com. Blackmer® is a leading brand of rotary vane and centrifugal pump and reciprocating compressor technologies from PSG. PSG, a Dover company, is comprised of several leading pump brands, including Abaque®, All-Flo, Almatec®, Blackmer®, Ebsray®, Griswold™, Mouvex®, Neptune™, Quattroflow™, RedScrew™ and Wilden®. For more information on Blackmer or PSG, please go to blackmer.com or psgdover.com.
The Rockville Propane Terminal is an undeniable American success story thanks to the ability of people like Pat Wenner, President of Rockville Propane Terminal, to recognize and take advantage of some significant shifts in the propane-supply and -distribution market in Minnesota. Aiding in this success are the Blackmer® LB601 Series Reciprocating Gas Compressors and LGL4 Series Sliding Vane Pumps the company relies on to optimize railcar deliveries and loading of propane transports.
The expanded Rockville Propane Terminal features 10 rail-loading towers and 16 propane-storage tanks with a combined storage capacity of 620,000 gallons. A second loading island was also built, doubling the number of transports that could be loaded in any given day.
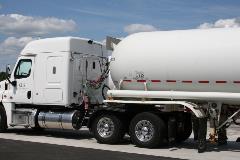
To make the expansion a reality, Wenner Gas Co., and CHS, Inc., created a partnership as a way to enhance storage and service capabilities at Wenner’s propane terminal. The partnership has been extremely successful and the terminal is now open 24/7 with more than enough capacity to serve the needs of its customers.
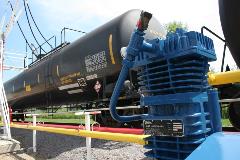
One constant in the growth of the Rockville Propane Terminal has been Wenner’s use and reliance on compressor technologies from Blackmer®. The terminal is currently using 10 LB601 Series Reciprocating Gas Compressors, which have had no problem keeping up with the unloading and loading rates that are required.
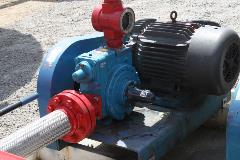
At its dual-transport loading island, Rockville Propane Terminal utilizes LGL4 Series Sliding Vane Pumps from Blackmer®. Designed for maximum performance and reliability, LGL4 pumps incorporate a wide variety of design features that help eliminate maintenance and downtime.
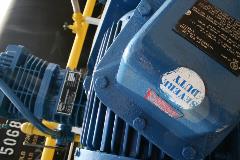
Blackmer® LB601 Series Reciprocating Gas Compressors feature ductile-iron construction that make them stronger and more resistant to thermal shock and corrosion than cast iron. This helps ensure efficient and reliable service under even the most severe operating conditions.
Pat Wenner, right, President of Rockville Propane Terminal, couldn’t be happier with the Blackmer® compressors and pump equipment that Scott McClelland, left, Engineer at LPG & NH3 Supply, recommended for the new terminal.