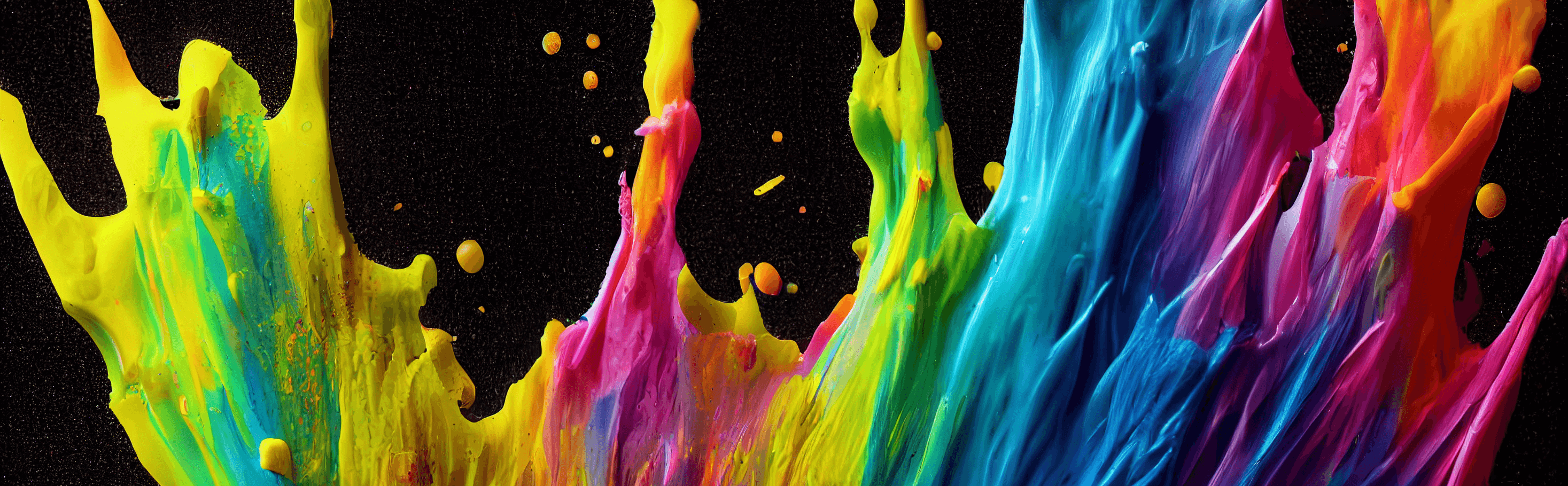
Liquid dosing plays a vital role in countless industries, from ensuring precise quantities in food and drink production, to guaranteeing consistent quality in polymer product manufacture. But beyond the intricate mechanics and technical specifications, there's an often-overlooked factor that can significantly impact the entire process: adding colour. In this blog, we’ll explore how you can achieve mess-free, easy and rapid colour changeovers that will save downtime and minimise the risk of spills with the help of Quantex disposable/single-pack-use pumps.
What is Liquid Dosing
Liquid dosing (also known as liquid metering) is the mixing of liquid solutions together to make a final product. There are many potential applications for this including:
- Food industry to add colour to food and drink products
- Food industry to add fragrances and flavourings
- Household chemical industry to add dyes to detergent
- Perfume industry to add fragrances
- Plastic or printing industry to add colourant to products
- Petrochemical industry to dose additives like catalysts and odorants
The Importance of Colour
Colour can be added to a product to help with visual quality control. When installed as part of a liquid metering system, colour can act as a visual indicator for various aspects of the process, such as:
- Concentration Levels – Dyes or colourants can be added to liquids to indicate their concentration. For instance, a graduated shift in colour from blue to red might signify a decreasing concentration of a specific chemical in a solution. This allows for quick and easy identification of potential issues during production.
- Flow Visualisation – Coloured liquids can be particularly useful in visualising flow patterns within pipelines or metering equipment. This can help identify blockages, leaks, or uneven flow distribution, ensuring the smooth operation of the system.
- Component Differentiation – In complex systems with multiple liquids flowing simultaneously, colour coding can be a lifesaver. Assigning a distinct colour to each liquid stream allows for easy identification and avoids accidental mixing of incompatible substances.
- Maintaining Consistency – Colour as a Quality Control Tool
- Product Aesthetics – The final product needs to be a particular colour
When we look at adding colourant via liquid dosing, we need to first consider what the colourant composition will (likely) be made of:
- A highly concentrated liquid binder (carrier)
- Highly concentrated colour pigment
- Other additives such as process additives, stabilisers or similar materials
As the colourant will be added to a larger solution as part of the liquid dosing process, it’s often supplied in a highly concentrated version. However, unless handled correctly this colourant solution can be extremely messy and difficult to handle, making pack changeovers complicated and time-consuming.
Negatives of Adding Colourants via Liquid Dosing
There are a variety of potential pain points when adding colourant via liquid dosing that need to be considered:
- Accurate dosing - will the correct level of colourant be added
- Cross-contamination - will there be remnants of a previous colour in the mix
- Chemical reaction - will materials be mixed causing an undesired reaction
- Pack composition - how is the colourant added
- Pack end of life (EOL) - how does the pack get replaced once consumed (and how quickly can this be completed)
- Cleaning and maintenance - how messy or complicated will this be
As liquid colourant is highly concentrated, it can be challenging and messy to manage, especially between colour changeovers. When a partially full or empty pack is swapped out and replaced, any remnants of colour could be spilt, causing stains on machinery, equipment, products, or the maintenance crew. These product spills could be hazardous, but could also leave long-lasting, undesirable stains.
With Quantex pumps that attach directly to the pack, we dramatically reduce this risk making it much easier, safer, cleaner and quicker to handle liquid colourant.
Mess-Free Colour Changeovers
By using a Quantex pump to help supply the perfect colour during liquid dosing, you’ll also be selecting a pump that will save you valuable time, energy and costs. Our Bag-In-Box pumps can be attached to the product packaging filled with the colourant and are designed to be replaced along with each new pack. When the product is fully dispensed, the bag can simply be swapped in and out of a machine in a matter of seconds with minimal training and drips. This removes the need for the product to travel through any additional fixed machinery and the risk of potential spills and mess.
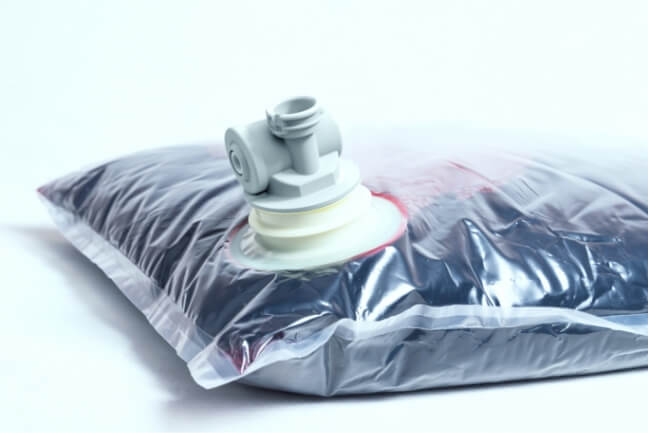
With only a standard motor drive and motor controller required, dispensing machinery can be highly compact and low-cost as no cleaning, maintenance and calibration is required. The pump acts as a check valve which keeps the liquid optimally hygienic and air-free, reducing the risk of product spoiling/ congealing. The pumps can reverse cycle to suck product back in at the end of each dispense which is how drips are prevented. This happens alongside the continuous benefit of our pumps removing the risk of pigments being contaminated during the liquid dosing procedure.
Accurate Levels of Colourant via Liquid Dosing
At Quantex, our range of pumps makes it possible for companies to dispense the correct amount of colour due to the unique method of precision pumping and in-pump dilution (when required). Within Quantex pumps, sits a fixed displacement pump design principle consisting of the volume of an individual cavity of liquid product carried on the rotor constrained within the rigid pump housing. This ensures that an accurate volume of liquid is displaced for each revolution over a wide range of flow rates, pressures, viscosities and temperatures.
By measuring and dosing the correct volume of colour to the mix, manufacturers can be assured that the final solution is the intended one, removing the risk of poor product quality.
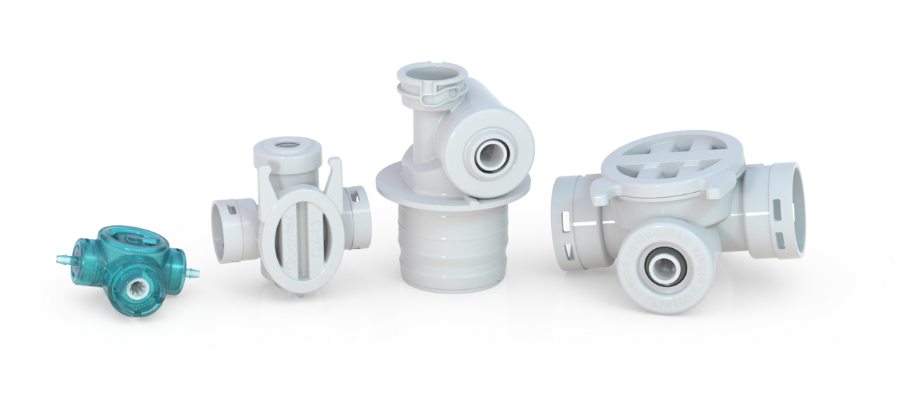
Another great benefit of Quantex pumps, is that they can outperform other pumps by propelling thick viscous solutions. This enables companies to take water out of the distribution channel and transfer concentrated solutions (reducing their carbon footprint and transportation costs).
Mixing Quantex with Colour
When it comes to adding colourants via liquid dosing with a Quantex pump, there are endless possibilities. A sample of the industries and potential usages of Quantex pumps include:
- Beauty and make-up brands - using our products to help clients match the perfect product with their skin tone.
- Polymer production - adding colour during the delivery of sustainable liquid dosing in the thermoplastic processes.
- Launderettes - who have a variety of dispensable cleaning solutions (of various concentrates) readily available at their fingertips.
- Emulsion paint suppliers - using a Quantex pump to help dispense the perfect colour to their paint without the risk of cross-contamination from heavy pigments.
Colour is a silent but crucial partner in the world of liquid dosing and liquid metering. By leveraging the power of Quantex pumps, companies can guarantee a mess-free, rapid colour changeover that’s also accurate and efficient during the manufacture of their liquid-based products.
To learn more about our pump range, please choose from the following options:
If you’d like to discuss how a Quantex pump could work for you, please email quantex-info@psgdover.com or call +49 (2065) 89205-0.